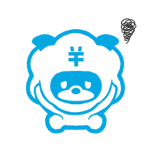
「図面の特記事項を見落として赤字になった」
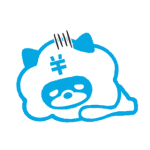
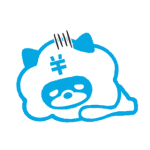
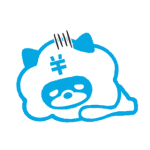
「ベテラン担当者の退職で見積もり精度が落ちた」
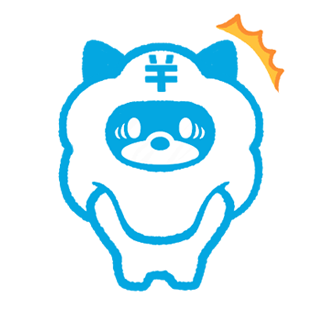
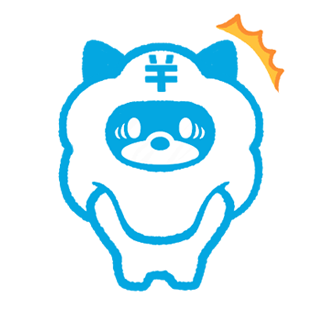
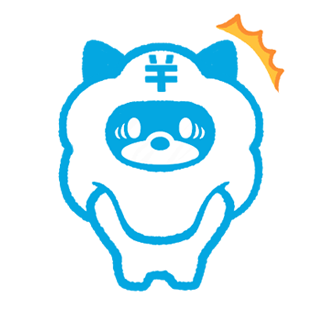
「設計変更が反映されず追加請求のクレームが増えた」
—こんな課題を抱えている製造業の方は少なくありません。実は、日本の製造業では見積もりの抜け漏れによって年間平均で売上の3〜8%もの損失が発生しているのです。
この記事では、製造業の見積もり業務における抜け漏れ問題とDXによる解決策について詳しく解説します。
この記事でわかること
- 図面からの見積もり抜け漏れが発生する具体的な原因
- 属人化した見積もりプロセスのリスクと対策方法
- 月額5万円から始められるDXツールの選定ポイント
- 投資回収期間8ヶ月を実現した中小製造業の事例
- 見積もり精度を±15%から±5%に向上させる方法
中小企業の経営者・管理職の方、工数見積もりに悩むマネージャーの方、システム導入を検討しているIT部門責任者の方に特におすすめの内容です。
コスト削減と業務効率化を同時に実現するDXの具体的手法を知りたい方は、ぜひご覧ください!
製造業DXで解決!図面からの見積もり抜け漏れを防ぐ方法
製造業における見積もり抜け漏れの現状と課題
見積もり抜け漏れが引き起こす損失と影響
製造業において、見積もりの抜け漏れは単なる事務的ミスではなく、企業の収益性を直接脅かす重大な問題です。
特に図面から情報を読み取る過程での見落としは、後工程になるほど修正コストが膨らみ、最悪の場合は赤字受注につながります。ある中小製造業では、図面の特記事項を見落としたことで特殊加工が必要となり、予定利益がゼロになってしまったケースもあります。
また、見積もりの精度低下は顧客との信頼関係にも影響します。追加請求の発生や納期遅延は、取引継続の障害となり、長期的な事業機会の損失にもつながるのです。
図面管理と見積もり精度の関係性
図面は製造業における見積もりの出発点であり、その管理状態が見積もり精度に直結します。多くの企業では、以下のような問題が見られます。
- 図面の版管理の不備:最新版ではない図面を基に見積もりを行い、設計変更点が反映されない
- 図面の分散管理:部門ごとに異なる場所・方法で図面を保管し、最新情報の共有が困難
- 図面情報の解釈ばらつき:同じ図面でも担当者によって読み取り方が異なる
ある調査によれば、製造業の見積もりエラーの約40%は図面管理の問題に起因しているとされています。特に設計変更が頻繁に発生するプロジェクトでは、図面の更新情報が見積もり担当者に正確に伝わらないことで、大きな見積もり誤差が生じるケースが多発しています。
中小製造業が直面する特有の課題
中小製造業では、大企業と比較して以下のような特有の課題に直面しています。
- 限られた人的リソース:専任の見積もり担当者を配置できず、兼任者の経験と勘に依存
- システム投資の制約:高額な図面管理・見積もりシステムの導入が困難
- 属人化の進行:熟練者の暗黙知に依存した見積もりプロセスが標準化されていない
- 多品種少量生産の増加:顧客ニーズの多様化に伴い、見積もり案件も複雑化
特に近年、働き方改革や人材不足の影響で、ベテラン社員の知識継承が課題となっています。あるアンケート調査では、中小製造業の約65%が「見積もりプロセスの属人化」を経営リスクとして認識しているという結果が出ています。
図面からの見積もり抜け漏れが発生する主な原因
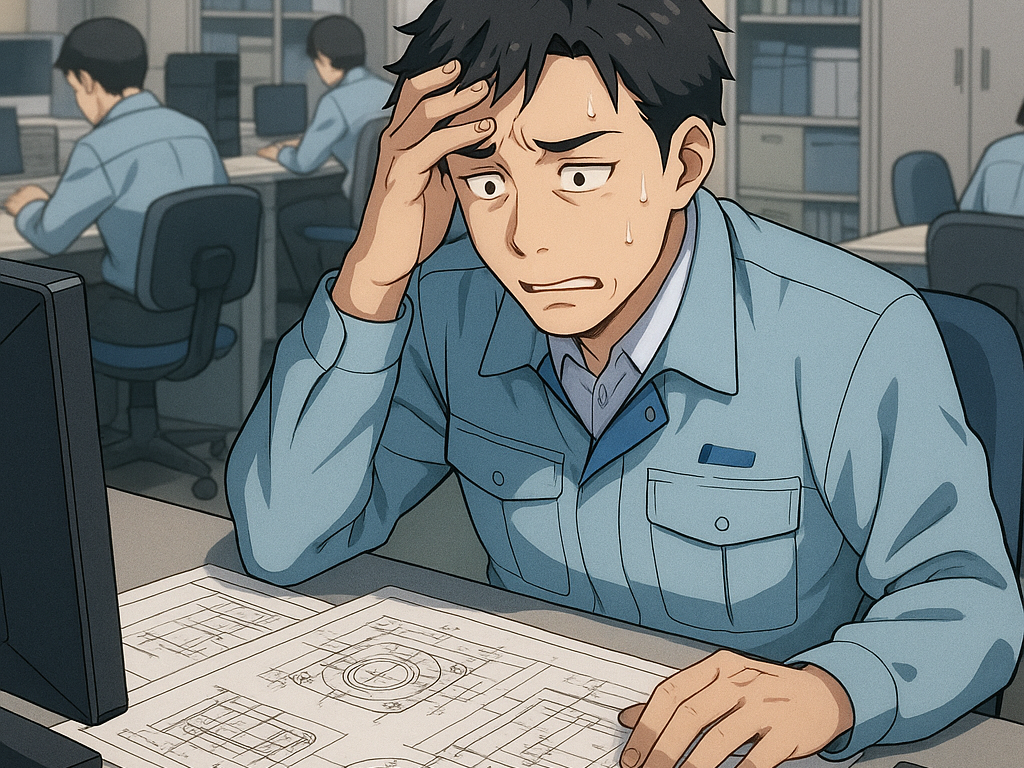
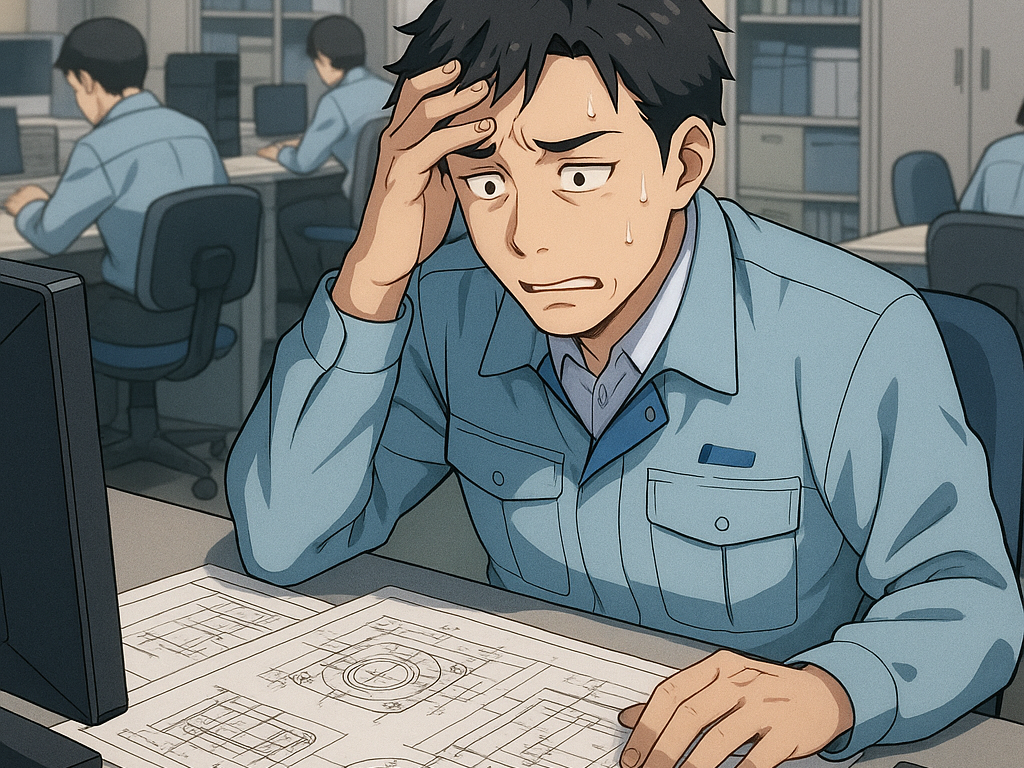
複雑な図面解釈ミスによる情報抽出エラー
製造業において図面は「言語」とも言えるものですが、その解釈には高度な専門知識と経験が必要です。ある機械部品メーカーの分析によれば、見積もりエラーの約35%は図面の注記見落としによるもので、特に「図面の端に小さく記載された表面処理要求」の見落としが最も多いとされています。
見積もり抜け漏れの主な原因としては、まず「注記・特記事項の見落とし」が挙げられます。
図面の余白や別紙に記載された特殊加工や表面処理などの情報を見逃すことで、後工程で追加工が必要になり、予定外のコストが発生してしまいます。
次に「公差・精度要求の見落とし」も頻発するミスです。
高精度加工が必要な箇所を見落とし、通常加工として見積もりを行うと、実際の加工では高額な工具や特殊な設備が必要になり、原価が大きく膨らむことになります。「複雑な形状の工数見積もりミス」も見逃せません。特に3D形状の加工難易度を過小評価してしまうと、実際の加工時間が見積もりを大幅に上回り、利益が圧迫される結果となります。
また「材料仕様の誤認」も重大な問題です。特殊材料や代替不可の指定を見落とし、標準材料で見積もりを行うと、材料費の差額だけでなく、特殊材料の調達期間による納期遅延も発生しかねません。
これらの図面解釈ミスは、ベテラン担当者でも起こりうるものです。属人的な見積もりプロセスからの脱却と、デジタル技術を活用した情報抽出の標準化が、製造業の競争力維持に不可欠となっているのです。
設計変更の反映漏れと版管理の問題
製品開発プロセスでは、設計変更は日常的に発生します。この変更情報が適切に管理・共有されないと、見積もりの抜け漏れにつながります。
- 設計変更の通知不足:設計部門から見積もり部門への変更連絡が不十分
- 図面の版管理不備:複数バージョンの図面が混在し、最新版が特定できない
- 変更履歴の不明確さ:何がどう変更されたかの情報が不明確で見落としやすい
- 関連図面の更新漏れ:一部の図面は更新されたが、関連図面の更新が漏れている
製造業の現場調査によると、設計変更に起因する見積もりエラーは全体の約30%を占め、特に複数部品から構成される製品では、一部品の変更が全体コストに与える影響の見積もりミスが多発しています。
属人的な見積もりプロセスのリスク
多くの中小製造業では、見積もりプロセスが特定の熟練者の経験と知識に依存する「属人化」が進んでいます。ある工作機械部品メーカーの調査では、同一図面に対する見積もり結果が担当者間で最大30%も異なるケースが報告されており、この属人化がもたらすリスクは想像以上に深刻です。
まず最も顕著なのが「担当者による精度のばらつき」です。同じ図面でも担当者によって見積もり結果が大きく異なることで、営業戦略の一貫性が損なわれるだけでなく、顧客からの信頼も揺らぎかねません。
次に「暗黙知への依存」の問題があります。「この形状ならこれくらいの工数」といった経験則が文書化されておらず、ベテラン社員の頭の中にだけ存在する知識に頼った見積もりが行われています。これは企業にとって大きなリスク要因となっています。
さらに深刻なのが「知識継承の断絶」です。ベテラン社員の退職により、長年培ってきた見積もりノウハウが一夜にして失われてしまうケースが増加しています。特に2025年問題※を控え、多くの企業がこの課題に直面しています。
※団塊の世代(1947~1949年生まれ)が75歳以上となり、国民の約5人に1人が後期高齢者となる超高齢化社会を迎えることで生じる社会問題の総称
また見落としがちなのが「繁忙期の精度低下」です。多忙時には確認プロセスが簡略化され、通常なら気づくはずの抜け漏れが増加します。特に受注が集中する時期こそ、正確な見積もりが利益確保に不可欠なのですが、皮肉にもそのような時期に精度が落ちやすいのです。
DXによる見積もり精度向上と抜け漏れ防止の方法
図面データのデジタル化と一元管理システム
見積もり精度向上の第一歩は、図面のデジタル化と一元管理です。
具体的には以下のようなアプローチが効果的です。
ある金属加工メーカーでは、クラウド型の図面管理システムを導入することで、図面の検索時間を平均15分から30秒に短縮し、最新版の図面を確実に参照できるようになったことで、設計変更の見落としによる見積もりエラーを80%削減することに成功しました。
AIを活用した図面読み取り技術の実際
製造業の見積もり業務において、AIの活用が革命的な変化をもたらしています。先進的な製造業では、AI図面読取りシステムを導入することで、図面からの情報抽出時間を90%削減し、見落とし率を75%低減させた事例が報告されており、特に標準的な機械部品においては、AIによる認識精度が95%を超えるケースも出てきています。
この進化を支えているのが、まず「OCR技術による注記の自動抽出」です。従来は人間が目視で確認していた図面上の文字情報を自動認識し、重要な注記や特記事項を漏れなく抽出することで、見積もりの精度向上に大きく貢献しています。特に図面の端に小さく記載された表面処理要求など、見落としやすい情報も確実に捉えることができます。
また「機械学習による類似部品の認識」も画期的な機能です。過去の図面データベースから類似形状を自動検出し、過去の見積もりデータを参照することで、経験の浅い担当者でも熟練者レベルの見積もり精度を実現できるようになりました。これにより属人化の解消と知識継承の問題も同時に解決できます。
さらに「自然言語処理による仕様書解析」技術により、図面に付随する仕様書から重要要件を自動抽出することが可能になりました。膨大なテキスト情報から加工条件や品質要求などの重要情報だけを瞬時に抽出し、見積もりに反映させることができます。
加えて「異常検知アルゴリズムによる矛盾点検出」機能は、図面情報と部品表の不一致など、人間では見落としがちな矛盾点を自動的に検出します。これにより、設計変更の反映漏れなどによる見積もりミスを未然に防ぐことができます。
これらのAI技術は、単なる業務効率化だけでなく、見積もり精度の向上による利益率改善、さらには顧客満足度向上にもつながっています。中小製造業においても、クラウドベースのAIサービスを活用することで、比較的低コストでこれらの技術を導入できる時代になりつつあります。製造業DXの第一歩として、図面読取りのAI化は最も費用対効果の高い選択肢の一つと言えるでしょう。
クラウドベースの見積もりシステム導入効果
クラウドベースの見積もりシステムは、中小製造業でも比較的低コストで導入でき、以下のような効果が期待できます。
・テンプレート活用による標準化
製品カテゴリごとの見積もりテンプレートを整備し、抜け漏れを防止
・チェックリスト機能
図面確認項目を体系化したチェックリストで見落としを防止
・過去案件データの参照機能
類似製品の見積もり実績を参照し、精度を向上
・部門間連携の強化
設計・製造・営業部門が同じプラットフォーム上で情報共有
ある精密部品メーカーでは、クラウド型見積もりシステムを導入することで、見積もり作成時間を平均60%削減し、見積もり精度(実際の原価との乖離)を従来の±15%から±5%に向上させることに成功しました。また、営業部門と技術部門の連携がスムーズになり、顧客からの見積もり依頼への回答時間も平均2日から半日に短縮されています。
中小製造業でも実現可能なDX導入ステップ
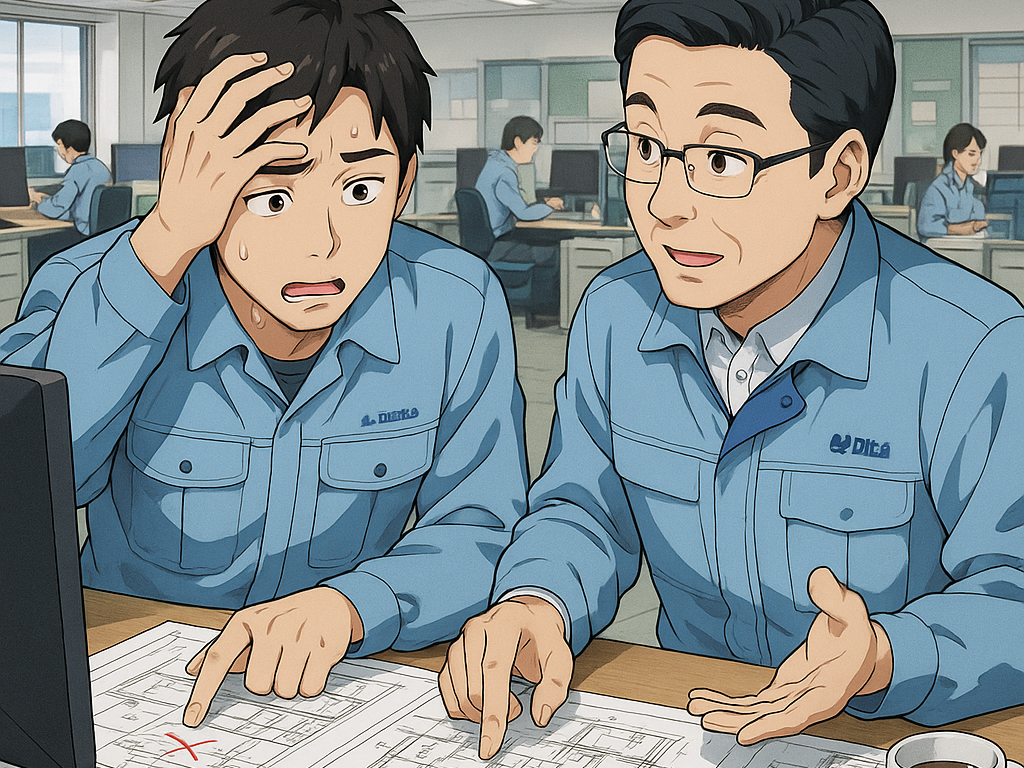
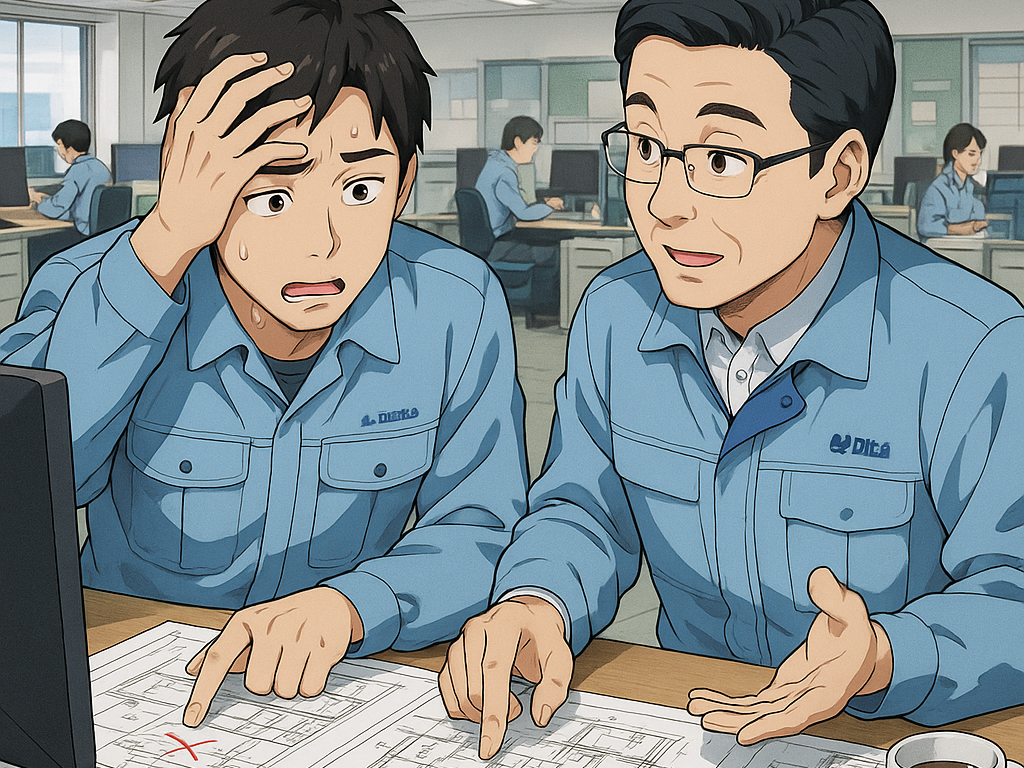
現状分析と課題の可視化手法
製造業のDX導入において、多くの企業が陥りがちな罠は「とりあえず最新システムを導入する」という思考です。しかし、真に効果的なDXの第一歩は、現状の見積もりプロセスを詳細に分析し、課題を可視化することから始まります。ある金型メーカーの成功事例では、見積もりプロセスの徹底分析により「複雑形状の加工時間見積もり」と「材料歩留まり計算」に最も大きなばらつきがあることを特定し、この2点に特化したデジタルツールを導入することで、効率的な改善を実現しました。
この事例が示すように、効果的な分析の第一ステップは「プロセスマッピング」です。図面受領から見積書作成までの全工程をフローチャート化することで、業務の全体像を把握し、各ステップの所要時間や関与する部門・担当者を明確にします。これにより、これまで「当たり前」と思われていた非効率なプロセスが浮き彫りになることも少なくありません。
次に重要なのが「エラー分析」です。過去1〜2年の見積もりミスを詳細に分類・集計し、発生頻度と影響度(金額的損失)を評価します。この分析により、「頻度は低いが一度発生すると大きな損失につながるエラー」と「頻度は高いが影響は小さいエラー」を区別し、優先的に対処すべき課題が明確になります。
さらに「ボトルネック特定」では、工数がかかる工程や情報の滞留が発生する箇所を特定します。例えば、図面の検索に平均15分かかっている、承認プロセスで書類が2日間滞留しているなど、業務の流れを妨げている箇所を特定することで、改善の糸口が見えてきます。
最後に「ROI試算」により、各課題解決によって得られる効果を金額換算します。例えば、見積もり時間の短縮による人件費削減額、見積もり精度向上による損失回避額、回答時間短縮による受注率向上効果などを試算し、投資判断の材料とします。
このように、DX導入前の徹底した現状分析は、限られた予算で最大の効果を得るための必須プロセスです。「何となく効率が悪い」という漠然とした認識から、「ここを改善すれば年間○○万円の効果が見込める」という具体的な投資判断へと昇華させることが、中小製造業のDX成功への近道と言えるでしょう。
段階的なシステム導入アプローチ
中小製造業では、一度に全システムを刷新するのではなく、段階的なアプローチが効果的です。
・図面のデジタル化と基本的なファイル管理システムの導入
・見積もりプロセスの標準化とチェックリスト作成
・クラウド型図面管理システムの導入
・標準部品・定型見積もり用のデータベース構築
・図面管理と見積もりシステムの連携
・AI技術の部分的導入(類似図面検索など)
・全社的なデータ連携(設計・製造・販売・会計)
・予測分析や自動見積もり機能の拡充
ある精密機械部品メーカーでは、この段階的アプローチにより、初年度は月額5万円程度のクラウドサービスから始め、3年かけて全社的なDXを実現。各フェーズで成果を確認しながら進めることで、社内の抵抗感も最小限に抑えることができました。
低コストで始められるDXツール選定ポイント
「DXは大企業のもの」という思い込みを捨てましょう。限られた予算でも効果的なDXを推進することは十分可能です。ある板金加工業者は、無料のクラウドストレージと表計算ソフトを組み合わせた簡易システムから始め、効果を確認しながら徐々に専門システムへ移行するアプローチで、総投資額を当初計画の半分に抑えることに成功しました。このような成功事例の背景には、賢明なツール選定があります。
まず重視すべきは「サブスクリプション型サービスの活用」です。初期投資を抑え、月額課金で利用できるSaaS(Software as a Service)を選択することで、資金繰りの厳しい中小企業でも無理なく導入できます。例えば、月額3〜5万円から始められるクラウド型図面管理サービスや、1ユーザーあたり月額5,000円程度の見積もりシステムなど、手頃な価格のサービスが増えています。
次に「必要最小限の機能から開始」する姿勢も重要です。オールインワンパッケージではなく、自社の課題解決に直結する機能に絞ったシンプルなツールから始めることで、コストを抑えるだけでなく、社内の習熟度も高めやすくなります。最初から完璧なシステムを目指すのではなく、「小さく始めて大きく育てる」発想が成功への近道です。
また長期的な視点では「拡張性の確認」も欠かせません。将来的な機能追加や他システムとの連携が可能なオープンなプラットフォームを選ぶことで、事業成長に合わせてシステムも成長させることができます。APIが公開されているか、データのエクスポート形式は標準的かなど、将来の発展性を見据えた選定が重要です。
さらに「無料トライアル期間の活用」も賢明な戦略です。実際の業務で試用し、効果を検証してから本導入することで、ミスマッチによる投資ロスを防げます。多くのクラウドサービスは14日〜30日の無料トライアル期間を設けており、この期間に自社の業務フローとの適合性を十分に確認しましょう。
最後に見落としがちなのが「サポート体制の充実度」です。導入支援や技術サポートが充実したベンダーを選定することで、ITリテラシーに不安がある中小製造業でもスムーズな導入が可能になります。特に日本語マニュアルの有無、問い合わせ対応の迅速さ、導入事例の豊富さなどは重要な判断材料となります。
これらのポイントを押さえたツール選定により、中小製造業でも「身の丈に合った」DXを実現し、段階的に効果を高めていくことが可能です。重要なのは「完璧を目指さない」こと。まずは小さな成功体験を積み重ね、組織全体のDXマインドを醸成していくアプローチが、持続可能なデジタル化への道筋となるでしょう。
図面管理システム導入による見積もり業務の改善事例
中小製造業における成功事例と効果
実際に図面管理システムを導入した中小製造業の成功事例をいくつかご紹介します。
精密部品メーカーA社 (従業員50名) | 板金加工業B社 (従業員30名) | 金型製造C社 (従業員80名) | |
---|---|---|---|
課題 | 図面の版管理不備による 見積もりミスが月平均3件発生 | ベテラン見積もり担当者の 退職に伴う知識継承問題 | 複雑形状の加工時間見積もりの ばらつきが大きい |
導入システム | クラウド型図面管理システム + 見積もりデータベース | AI搭載の図面解析ツール + 見積もりテンプレート | 3D CADデータ連携型の 工数見積もりシステム |
効果 | 見積もりミスが月平均0.3件に 減少(90%削減)、 顧客からのクレーム60%減少 | 新任担当者でも2週間の研修で 80%の精度の見積もりが可能に、 見積もり回答時間が 平均2日から4時間に短縮 | 見積もり精度が±20%から ±8%に向上、受注率が15%向上 |
これらの事例に共通するのは、単にシステムを導入しただけでなく、業務プロセスの見直しや社員教育を並行して実施している点です。
見積もり工数削減と精度向上の実績数値
図面管理と見積もりシステムの連携による具体的な効果を数値で見てみましょう。
- 図面検索時間:平均12分 → 30秒(96%削減)
- 見積書作成時間:平均45分 → 15分(67%削減)
- 見積もり承認プロセス:平均2日 → 4時間(75%削減)
- 類似案件の参照:平均20分 → 2分(90%削減)
- 見積もり精度(実際原価との乖離):平均±15% → ±5%
- 見積もり抜け漏れ発生率:8.5% → 1.2%(86%減少)
- 追加請求発生率:12% → 3%(75%減少)
- 担当者間のばらつき:最大30% → 最大10%
ある調査によれば、図面管理と見積もりシステムを連携させた製造業では、平均して利益率が2.5%向上したという結果も報告されています。
ROI(投資対効果)の具体的分析
DX投資の経済効果を具体的に分析した事例を見てみましょう。
中規模プレス加工メーカーの事例(年商10億円)
初期投資
- クラウド型図面管理システム導入費:100万円
- 見積もりシステム導入費:150万円
- コンサルティング・教育費:80万円
- 初期データ移行費:70万円
▶合計:400万円
年間ランニングコスト
- システム利用料:60万円/年
- 保守・サポート費:30万円/年
▶合計:90万円/年
年間効果
- 見積もり工数削減効果:120万円/年
- 抜け漏れ防止による損失回避:350万円/年
- 受注率向上による売上増:300万円/年
▶合計:770万円/年
ROI分析
- 初年度ROI:(770万円 – 400万円 – 90万円) ÷ 400万円 = 70%
- 2年目以降ROI:(770万円 – 90万円) ÷ 400万円 = 170%
- 投資回収期間:約8ヶ月
この事例では、初期投資が比較的大きいものの、8ヶ月程度で投資回収できており、2年目以降は大きなリターンが得られています。特に「抜け漏れ防止による損失回避」の効果が大きく、DX投資の価値を示しています。
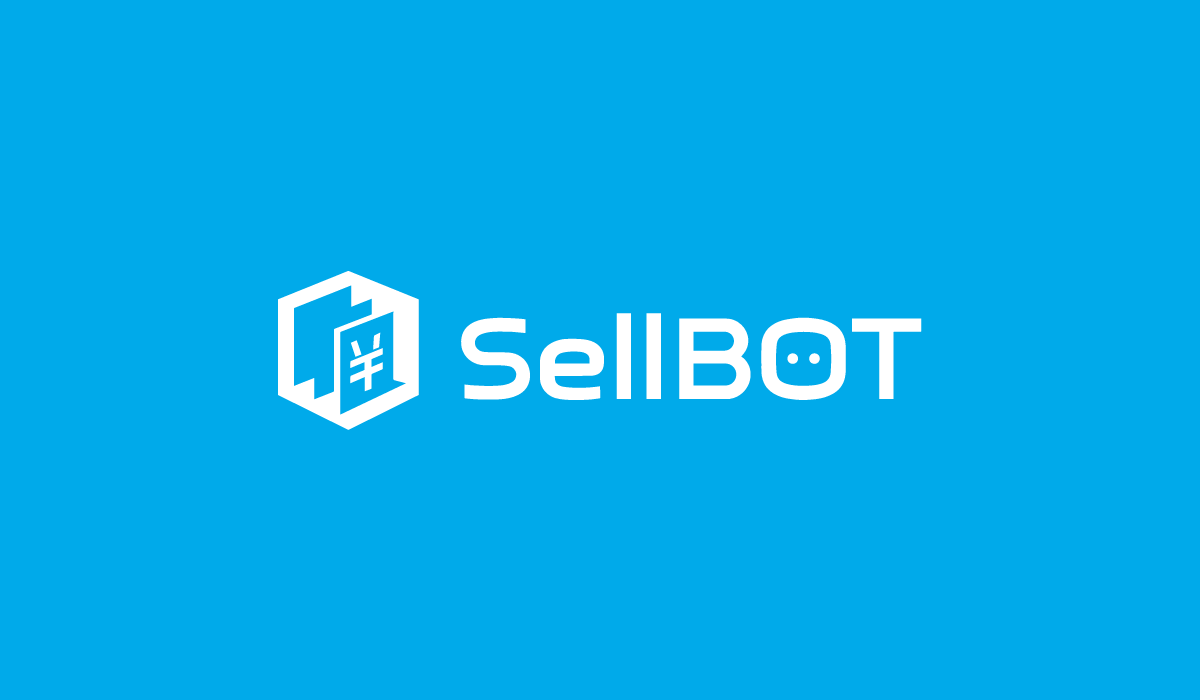
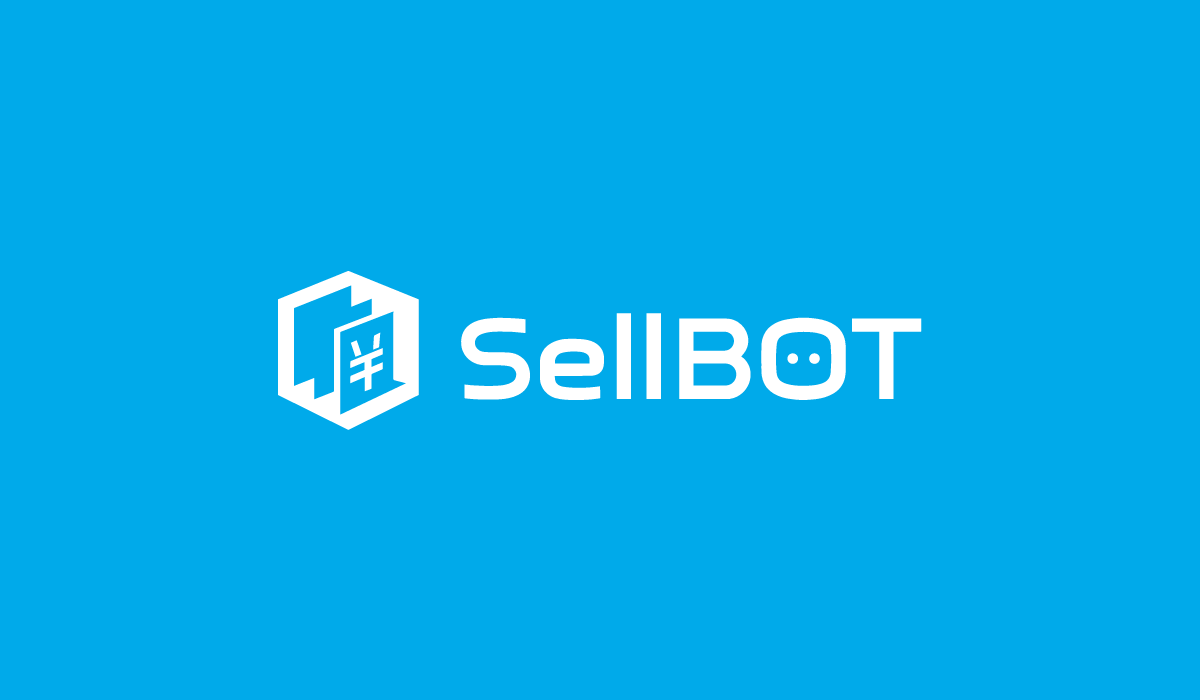
見積もり抜け漏れを防止するための組織体制と人材育成
見積もりプロセスの標準化と知識共有の仕組み
製造業のDXにおいて見落としがちなのが「人と組織」の改革です。システム導入だけでは真の効果は得られません。
ある自動車部品メーカーの成功事例は、この点を如実に物語っています。同社では、見積もりプロセスを標準化し、チェックリストを整備することで、新人でも3ヶ月で一人前の見積もり担当者として機能できるようになり、人材育成期間を従来の1/3に短縮することに成功しました。この事例が示すように、システム導入と並行した組織的な取り組みが、DX成功の鍵を握っています。
まず基盤となるのが「見積もり標準手順書(SOP)の整備」です。図面確認の基本ステップを文書化し、製品カテゴリ別のチェックポイントを明確化することで、担当者による見積もり精度のばらつきを最小化できます。特に注意すべき特殊仕様・加工を一覧化しておくことで、経験の浅い担当者でも重要ポイントを見落とすリスクを大幅に減らせます。SOPは単なるマニュアルではなく、組織の知恵を結集した「判断基準」として機能させることが重要です。
次に欠かせないのが「ナレッジベースの構築」です。過去の見積もりミス事例とその対策をデータベース化することで、「同じ失敗を繰り返さない」組織文化を醸成できます。特に重要なのは、ベテラン社員の暗黙知を形式知化する取り組みです。「なぜこの加工にはこれだけの工数が必要か」といった経験則を動画やマニュアルに落とし込むことで、退職によるノウハウ流出を防ぎます。さらにFAQ形式での検索可能な知識共有システムを構築することで、必要な情報に素早くアクセスできる環境を整えましょう。
そして見積もり品質を持続的に高めるための「見積もりレビュープロセスの確立」も重要です。複数人によるクロスチェック体制を整え、金額規模に応じた承認フローを設定することで、重要案件ほど慎重な検証が行われる仕組みを作ります。また定期的な見積もり精度の振り返りミーティングを実施することで、組織全体で継続的に改善するPDCAサイクルを回すことができます。
これらの取り組みは、一見するとDXとは無関係に思えるかもしれませんが、実はデジタル技術の効果を最大化するための土台となります。いくら高度なシステムを導入しても、それを活用する人と組織の仕組みが整っていなければ、期待した効果は得られません。システムと人、テクノロジーと組織文化を両輪として進めることが、真の意味での製造業DXの成功への道筋となるのです。
デジタルツールを最大限活用するための教育方法
DXツールの効果を最大化するための教育アプローチとしては以下があげられます。
- 基本操作から応用機能まで段階的に習得
- 実際の業務データを使った実践的な演習
- 定期的なスキルチェックとフォローアップ
- 短時間の動画マニュアル
- 操作手順を示すスクリーンショット集
- よくある質問と回答集
- システム活用の得意な社員をサポート役に任命
- 部門内での小グループ学習会
- 成功事例の共有会
ある精密機器メーカーでは、「デジタルバディ制度」を導入し、ITリテラシーの高い若手社員がベテラン社員のDXツール活用をサポートする仕組みを作ることで、世代間のギャップを埋めながら効果的な技術移転を実現しています。
部門間連携を強化するワークフロー改革
製造業の見積もり精度向上において最大の障壁となるのが、いわゆる「サイロ化」—部門間の壁です。
ある工作機械部品メーカーの革新的な取り組みは、この課題に真っ向から挑戦したものでした。
同社では、設計・製造・見積もり・営業の4部門が週1回30分の「見積もり精度向上ミーティング」を実施し、各部門の視点から見積もりプロセスを継続的に改善する取り組みを行っています。この結果、部門間の情報共有が活性化し、見積もり精度が平均15%向上したと報告されています。この成功事例が示すように、部門を超えた連携が見積もり精度向上の鍵を握っています。
まず重要なのが「設計-見積もり連携の強化」です。設計変更時の自動通知システムを導入することで、設計変更が即座に見積もり担当者に伝わる仕組みを構築します。また設計者と見積もり担当者の定期ミーティングを通じて、相互理解を深めることも効果的です。さらに一歩進んで、設計段階からのコスト検討プロセス(DTC: Design to Cost)を導入することで、設計時点から製造コストを意識した製品開発が可能になります。これにより、後工程での大幅な見積もり修正を減らすことができます。
次に「製造-見積もり連携の強化」も見積もり精度向上に大きく貢献します。実績データのフィードバックループを構築し、実際の製造時間と見積もり工数の差異を定期的に分析することで、見積もり精度を継続的に改善できます。また製造現場からの見積もり精度向上提案制度を設けることで、現場の知恵を見積もりに反映させる仕組みを作ります。さらに見積もり部門と製造部門が共同で原価低減活動に取り組むことで、コスト競争力と利益率の同時向上が期待できます。
そして「営業-見積もり連携の強化」も忘れてはなりません。顧客要求の正確な伝達プロセスを確立し、営業担当者が顧客から得た情報を漏れなく見積もり担当者に伝える仕組みを整えます。また見積もり根拠の可視化による提案力強化も重要です。原価構成を明確にすることで、営業担当者は顧客に対してより説得力のある提案が可能になります。さらに価格交渉のための原価データ活用により、値引き交渉の場面でも適切な判断ができるようになります。
これらの部門間連携は、単なる情報共有の枠を超え、企業全体の競争力強化につながる取り組みです。DXツールはこうした連携を支援する重要な役割を果たしますが、最も重要なのは「部門の壁を越えて協力する」という組織文化の醸成です。週30分のミーティングから始まった小さな変化が、やがて企業全体の体質改善につながる—製造業DXの本質は、こうした地道な取り組みの積み重ねにあるのかもしれません。
まとめ
製造業における見積もりの抜け漏れは、企業の収益性を直接脅かす重大な課題です。
特に図面からの情報抽出段階でのミスは、後工程になるほど修正コストが膨らみ、時には赤字受注の原因となることも少なくありません。
本記事では、製造業DXの観点から、図面管理と見積もりプロセスの改善方法について詳しく解説しました。ポイントをまとめると以下の通りです。
1:図面管理の一元化
最新図面へのアクセスを保証し、設計変更の見落としを防止
2:AIによる図面読取り支援
注記や特記事項の見落としを減らし、情報抽出を効率化
3:クラウド型システムの活用
初期投資を抑えつつ、部門間の情報共有を促進
4:段階的なDX推進
自社の状況に合わせた現実的なステップで着実に進める
5:組織的取り組みの重要性
システム導入だけでなく、プロセス改革と人材育成が不可欠
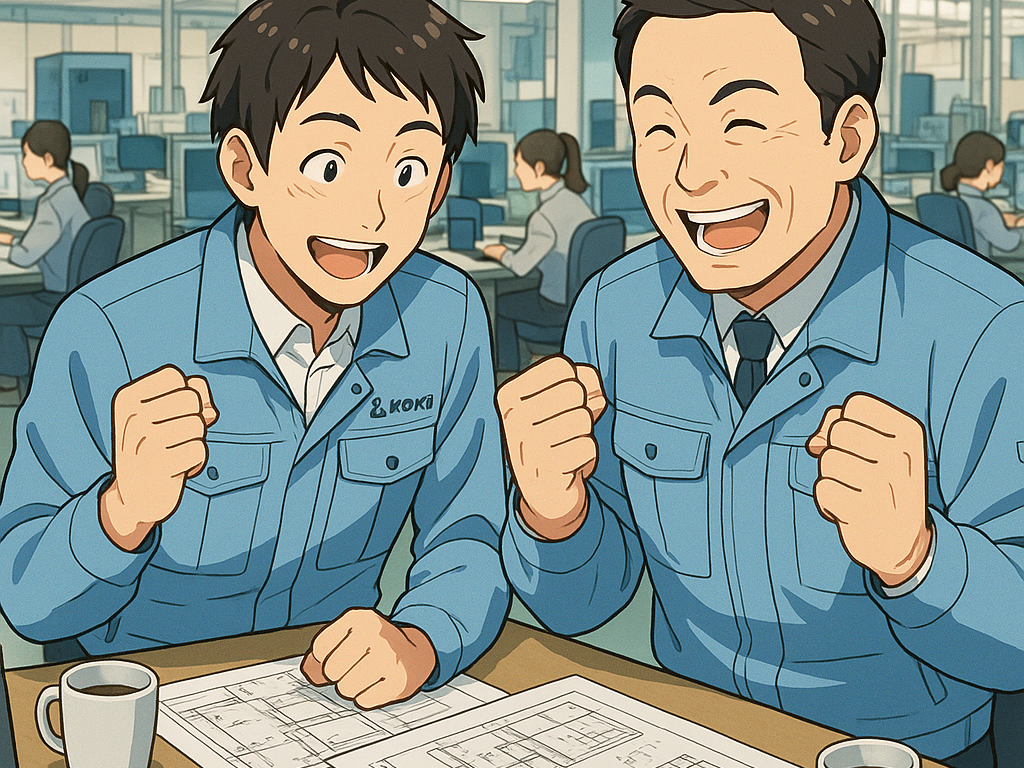
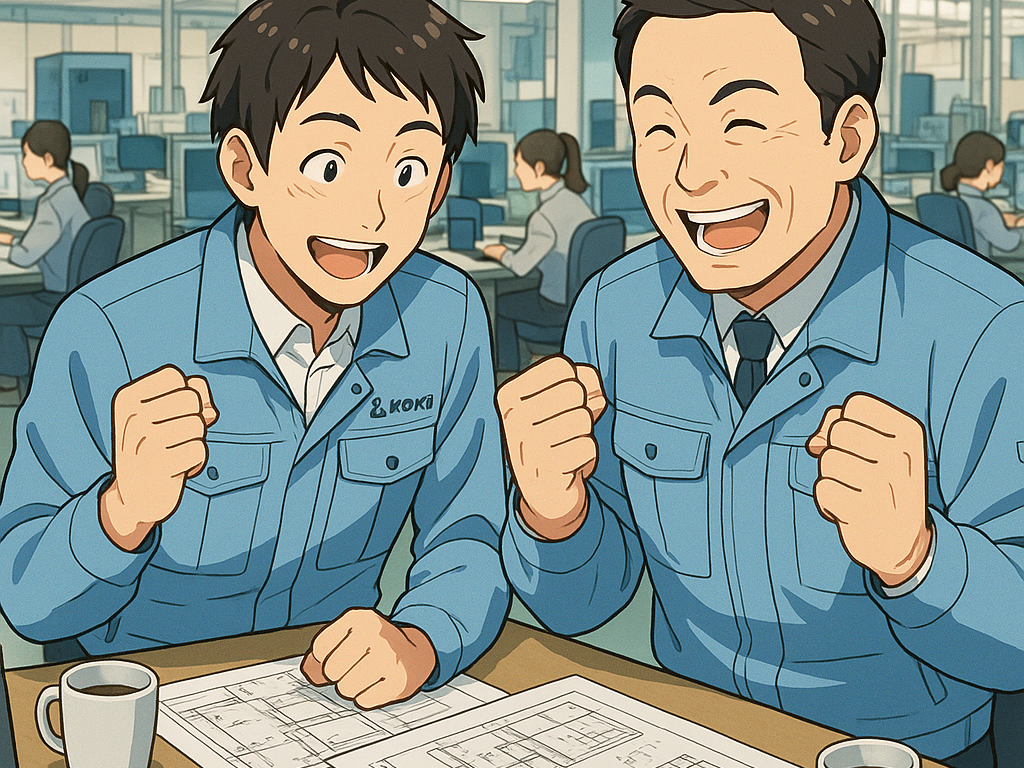
DXによる見積もり業務改革は、単なる効率化だけでなく、正確な原価把握による戦略的価格設定や、迅速な見積回答による顧客満足度向上など、多面的な競争力強化につながります。
中小製造業においても、本記事で紹介したような段階的アプローチと費用対効果の高いツール選定により、無理なくDXを推進することが可能です。見積もり業務の精度向上は、製造業の収益性改善と持続的成長の鍵となるでしょう。
見積もり抜け漏れゼロを目指したDXの取り組みが、御社の競争力強化と利益率向上につながることを願っています。