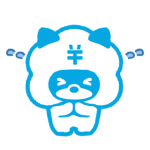
ベテランがどんどん定年で辞めていって、
若手に技術がなかなか伝わらない
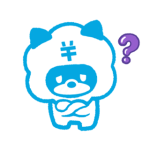
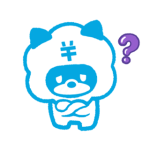
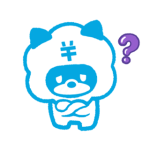
他社がどんな工夫をして
技術継承や生産性向上に取り組んでいるのか知りたい
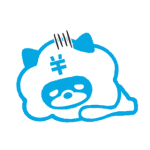
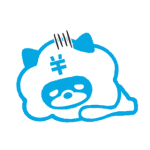
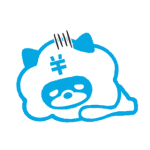
技術継承って、具体的に何から始めればいいのかわからない…
こんな悩みを解決します。
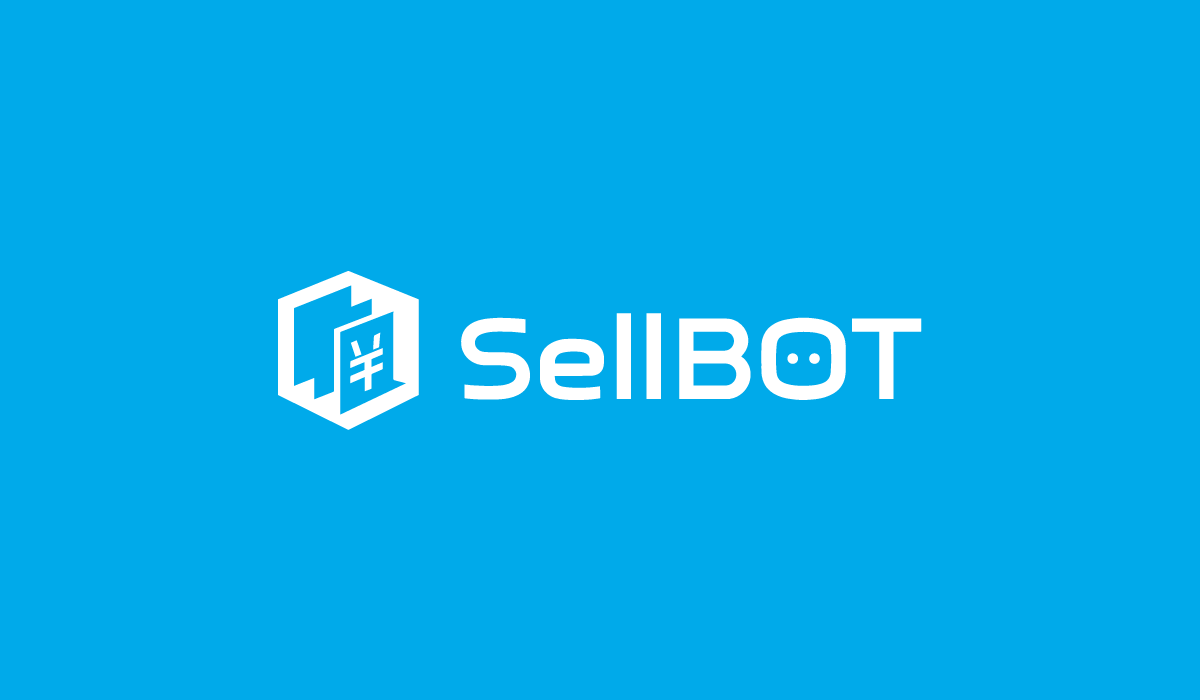
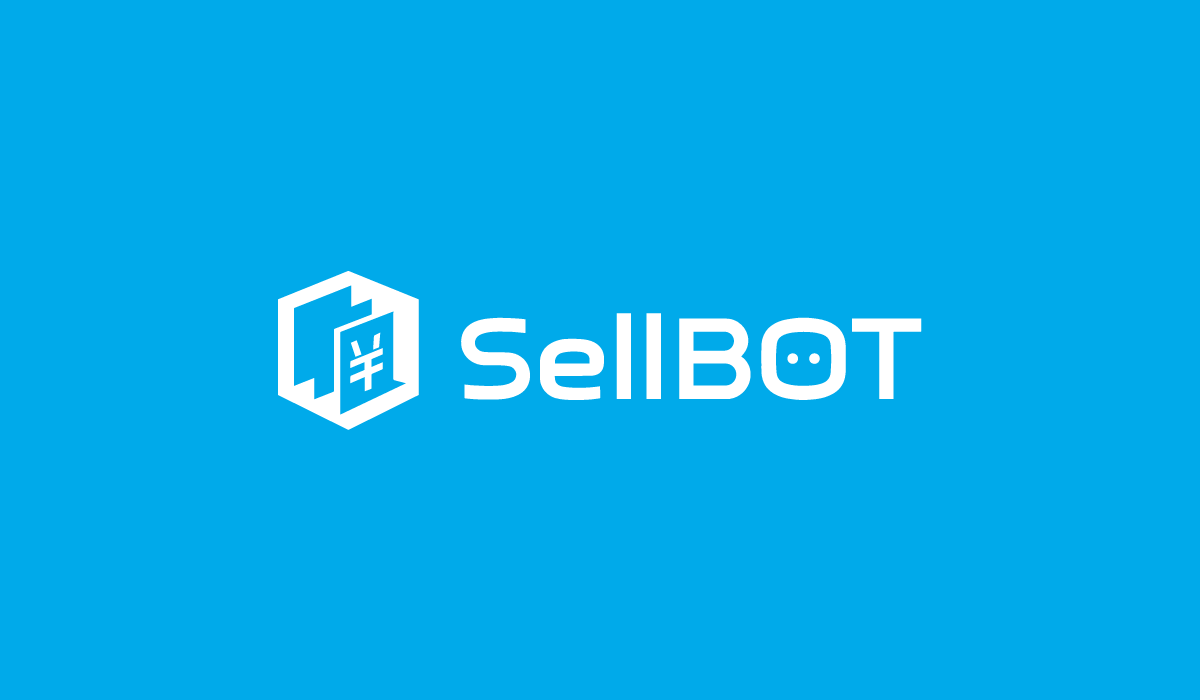
製造業の生産性向上を実現する、AI見積もり・類似図面検索システム「SellBOT(セルボット)」
- 図面をアップロードするだけで AIが自動見積もり
- 過去データから 類似図面を瞬時に検索
- 新旧図面の 差分を自動表示 してミスを撲滅
- 見積もり依頼~受注・発注まで EDIで一元管理
ベテラン頼みだった見積もり業務を“誰でも・すぐに・正確に”――。
貴社の技術継承と生産性向上を同時に推進します。
長年築き上げてきた技術やノウハウを次世代に伝えることは、製造業にとって永遠の課題ですよね。
特に機械・金属加工業では、職人の「カン」と「コツ」が品質や生産性を左右します。しかし、単に若手を育成するだけでは、激化する国際競争の中で生き残ることは難しくなっているのも事実。
そこで本記事では、熟練技術者の技術を「見える化」するのと同時に、生産性を向上させた製造業の成功事例をご紹介。さらに、デジタル技術を活用して技術継承と生産性向上を両立させ、企業の競争力を維持・強化するための実践的なアプローチまでご提案します。
貴社の貴重な技術資産を未来に繋ぎ、さらに、発展させるためのヒントが見つかるはずです。
本記事でわかること
- ベテランの技術を効率的に若手に継承する方法
- 他社の成功事例から学ぶ実践的な改善アプローチ
- 技術継承を始める具体的なステップ
- 限られた予算でも実現できる生産性改善の方法
- 現場の抵抗を乗り越えてDXを成功させる変革マネジメント方法
製造業が直面する生産性向上の課題とは
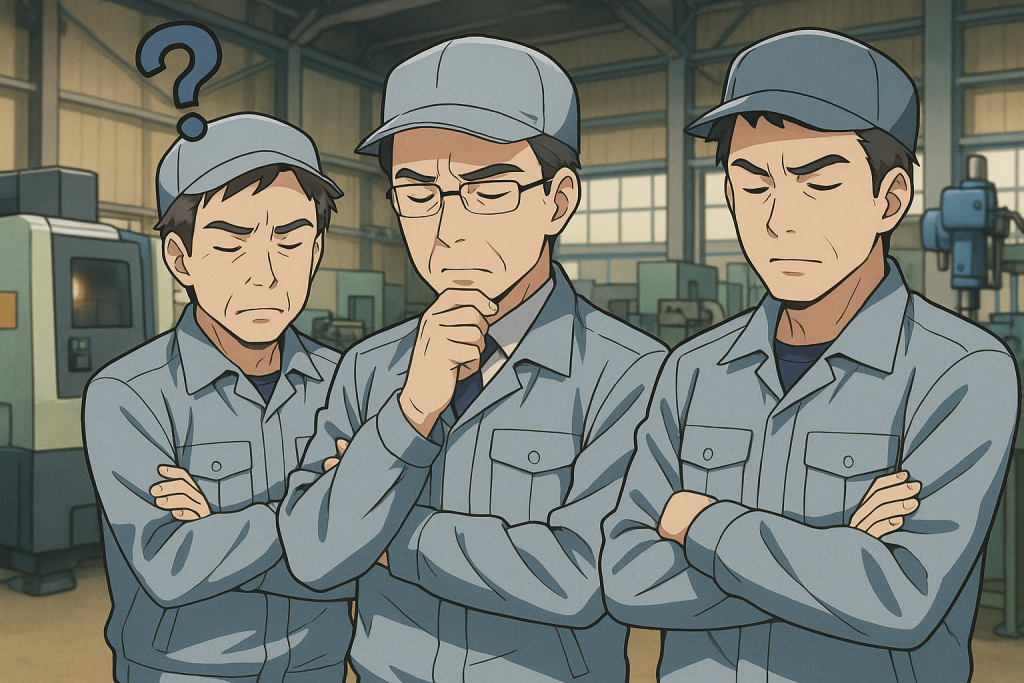
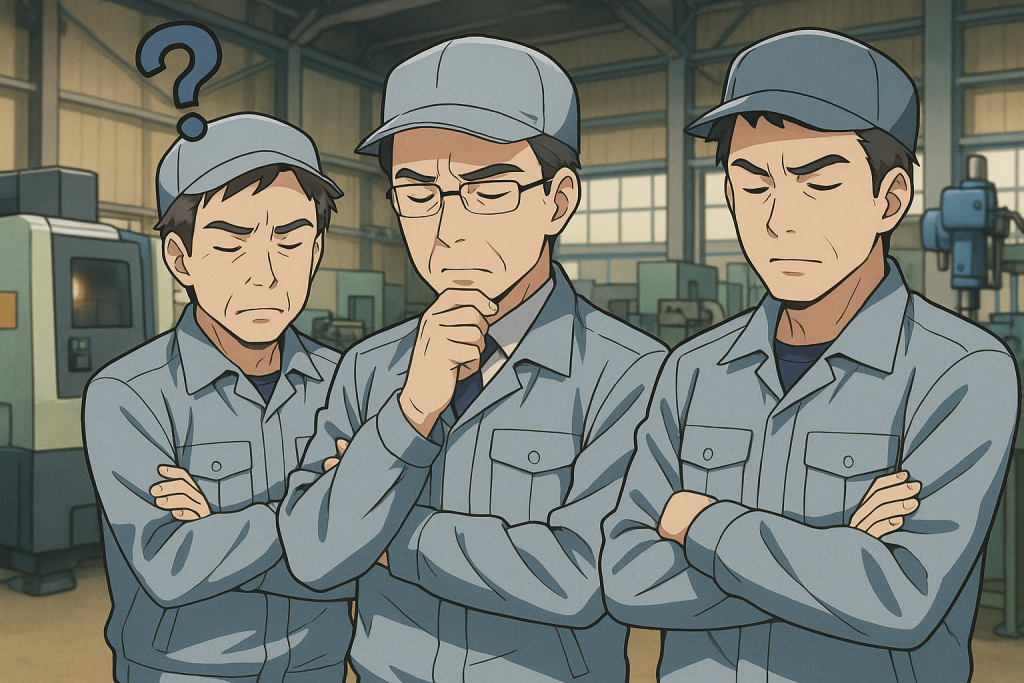
日本のものづくりを支えてきた製造業ですが、近年、国内外の厳しい競争環境や国内の構造的な課題に直面し、生産性の向上が急務となっています。特に中小製造業においては、大企業とは異なる特有の難しさも抱えています。
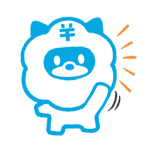
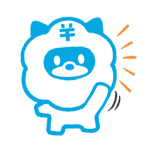
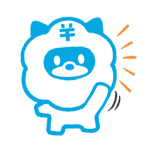
まずは、製造業がどのような課題に直面しているのか、現状を具体的に見ていきましょう。
日本の製造業における生産性の現状
長年にわたり、日本の製造業は高品質な製品を生み出すことで国際的な競争力を維持してきました。しかし、公益財団法人日本生産性本部が発表する「労働生産性の国際比較」などのデータを見ると、近年、日本の製造業の労働生産性は、他のOECD諸国と比較して必ずしも高い水準にあるとは言えない状況が続いています。
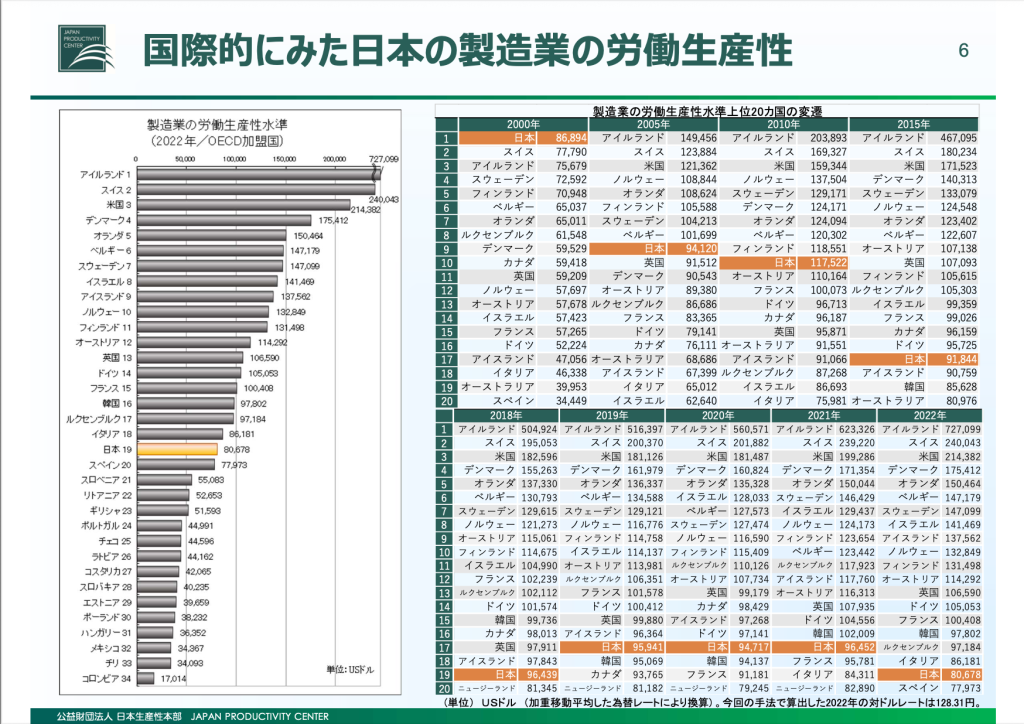
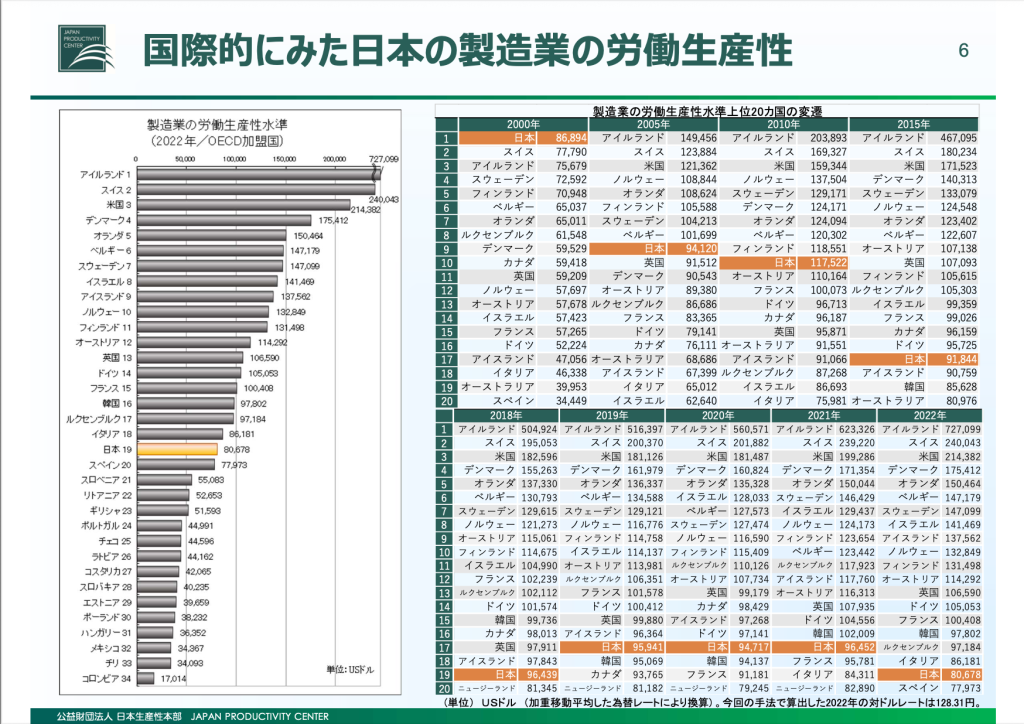
出典元:公益財団法人日本生産性本部
この背景には主に以下の要因があります。
- 少子高齢化による労働力人口の減少
- グローバル化の進展による価格競争の激化
- デジタル化への対応の遅れ
これら複数の要因が複雑に絡み合っており、特に従来型の大量生産モデルから、顧客ニーズの多様化に対応した多品種少量生産へのシフトが求められる中で、生産プロセス全体の効率化が追い付いていないケースが見られます。
熟練技術者の高齢化による技術継承の危機
製造現場における最も深刻な課題の一つが、長年にわたり日本のものづくりを支えてきた熟練技術者の高齢化と、それに伴う技術・技能の継承問題です。
機械・金属加工業においても、図面だけでは読み取れない勘所や、長年の経験で培われたノウハウは、一朝一夕には若手に伝えられるものではありません。
機械・金属加工の現場では、図面には書かれていない細かなポイントや、ベテランが長年かけて身につけた技術を新人にすぐに教えるのは難しいものです。
これらの貴重な「匠の技」が失われてしまうことは、単に一企業の損失に留まらず、日本の製造業全体の競争力低下にも繋がりかねません。
後継者不足も相まって、事業承継のタイミングで廃業を選択せざるを得ない企業も多く、この技術継承の課題をいかに乗り越えるかが、持続的な企業成長のための今すぐ取り組むべき課題となっています。
中小製造業が抱える生産性向上の壁
大企業と比較して、中小製造業が生産性向上に取り組む際には、特有の壁が存在します。
まず挙げられるのが、資金力の制約です。最新の設備投資や大規模なシステム導入には多額の費用が必要となり、中小企業にとっては大きな負担となります。
また、人材不足も深刻です。DX推進を担えるIT人材の採用が難しいだけでなく、現場の従業員も日々の業務に追われ、新たな取り組みに時間を割く余裕がないケースが多く見られます。
さらに、効果測定の難しさや、導入したツールの活用が進まないといった、「導入したものの、成果に繋がらない」という悩みも少なくありません。
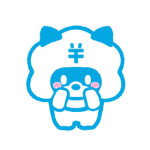
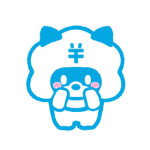
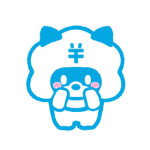
これらの壁を認識した上で、自社に合った現実的なステップで改善を進めることが重要です。
生産性向上がもたらす経営上のメリット
生産性向上は、単に現場の効率が上がるというだけでなく、企業経営全体に多大な好影響をもたらします。厳しい経営環境を乗り越え、持続的な成長を遂げるために、生産性向上がどのような経営上のメリットを生むのか具体的に見ていきましょう。
収益力と国際競争力の強化
生産性が向上すれば、同じリソース(人員、設備、時間)でより多くの製品を生み出す、あるいはより付加価値の高い製品を生み出すことが可能になります。
これにより、製品一つあたりのコストが削減され、収益性が向上し、捻出された利益は、さらなる設備投資や研究開発、人材育成に再投資することができ、企業の成長サイクルを加速させます。
また、国内市場が縮小傾向にある中で、海外市場への展開も視野に入れる企業にとっては、国際競争力の強化が不可欠です。品質を維持・向上させながらコスト競争力も高めることで、グローバルな市場においても優位性を確立しやすくなります。
このように、生産性向上は単なるコスト削減にとどまらず、企業の持続的成長と競争力強化を実現する重要な経営戦略と言えるでしょう。
ノウハウ“見える化”が生む継承コスト削減効果
熟練技術者の持つ言葉で説明しにくいノウハウや勘所をデジタル技術などを活用して「見える化」することは、技術継承の効率を飛躍的に高めます。
従来、OJT(On-the-Job Training:職場内訓練)に頼りがちだった技術指導も、標準化されたマニュアルやデータに基づいた教育が可能になることで、指導者側の負担軽減はもちろん、若手技術者が早期に戦力化することを助けます。
これにより、技術継承にかかる時間的コスト、人的コストを大幅に削減できる可能性があります。また、特定の個人に依存していた技術が組織の共有財産となることで、属人化のリスクも低減できます。
このように、技術の見える化は、効率的な技術継承、コスト削減、属人化リスクの解消を同時に実現し、組織全体の技術力向上と安定した事業運営を可能にします。
人手不足時代を乗り切る組織体制の構築
少子高齢化が進み、多くの産業で人手不足が深刻化する中、製造業も例外ではありません。限られた人材で高い生産性を維持し、事業を継続していくためには、より効率的な働き方ができる組織体制の構築が不可欠です。
生産性向上への取り組みは、単に機械化・自動化を進めるだけでなく、従業員一人ひとりの業務負荷を軽減し、より創造的な業務や高度な判断が求められる業務に集中できる環境を生み出します。
これにより、従業員のモチベーション向上や定着率の改善も期待でき、人手不足時代においても競争力を維持できる強靭な組織体制を築くことに繋がります。
このように、生産性向上は人手不足という課題を解決するだけでなく、従業員満足度の向上と組織力強化を両立させる、持続可能な経営戦略と言えるでしょう。
現場レベルで始める生産性改善の基本ステップ
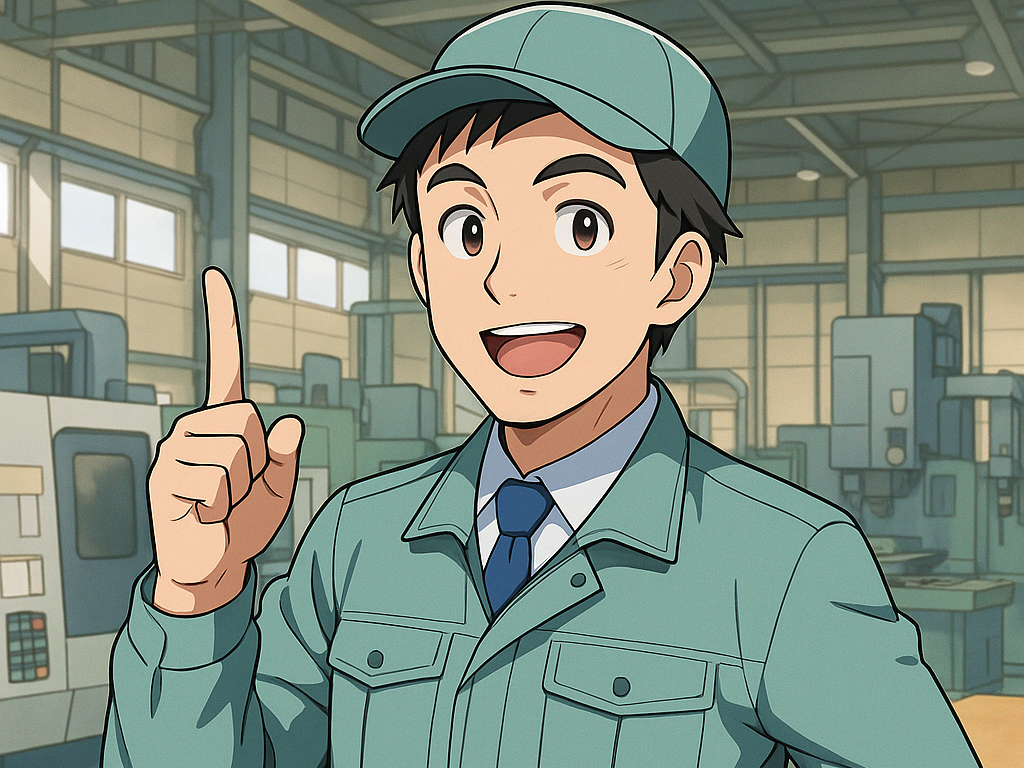
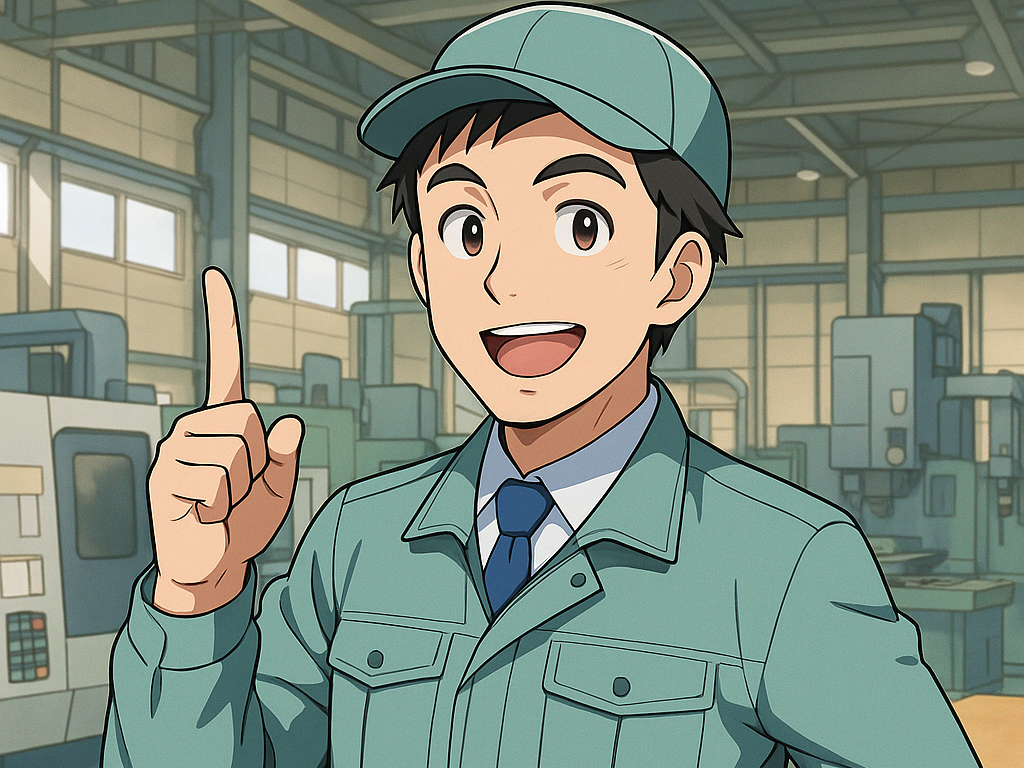
DXというと大規模な改革をイメージしがちですが、生産性改善はまず現場レベルでの地道な取り組みから始めることが重要です。
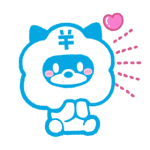
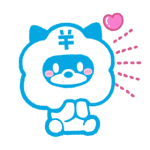
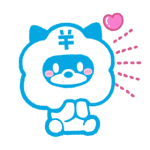
ここでは、アナログな手法も含めた、生産性改善の基本的なステップをご紹介します。
アナログ中心の現状分析と課題の可視化
最初に取り組むべきは、デジタルツールに頼る前に、まず現状の業務プロセスや課題を徹底的に「見える化」することです。
製造現場に足を運び、作業の様子を観察し、従業員へのヒアリングを通じて、どこに無駄があり、何が作業の妨げになっているのかを具体的に洗い出します。
この際、作業時間、手戻り回数、不良品率といったデータを手作業で記録・集計することも有効です。
アナログな手法であっても、現状を客観的に把握することが、的確な改善策を立案するための第一歩となります。
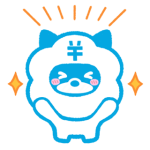
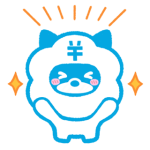
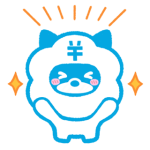
重要なのは、先入観を持たずに現場の声に耳を傾け、潜在的な課題まで掘り下げることです。
5S活動で整える改善の土台
生産性改善の基本中の基本であり、効果も大きいのが「5S活動」です。
5S活動とは、「整理(Seiri)」「整頓(Seiton)」「清掃(Seisou)」「清潔(Seiketsu)」「躾(Shitsuke)」の頭文字Sを取ったもので、職場環境を整え維持するための活動です。
一見地味に思えるかもしれませんが、5Sを徹底することで、探し物の時間が削減され、作業スペースが確保され、安全性が向上するなど、業務効率の向上に直結します。また、従業員一人ひとりが改善意識を持つきっかけとなり、生産性改善活動を進める上での強固な土台となります。
5Sは一度行ったら終わりではなく、継続的に取り組むことでその効果を持続させることが重要です。
このように、5S活動は単なる職場の整理整頓にとどまらず、業務効率向上と従業員の改善意識を高めることを両立させる、生産性改善の基盤となる重要な取り組みなのです。
ライン単位の標準化とPDCAサイクルの確立
現状分析と5S活動で土台が整ったら、次に個別の製造ラインや工程単位での作業標準化を進めます。
熟練技術者の動きや判断基準を基に、誰でも一定の品質で効率的に作業できるような標準作業手順書を作成し徹底します。これにより、作業品質のばらつきを抑え、新人でも早期に業務を習得できるようになります。
そして、標準化された作業を実践する中で、定期的に効果を測定・評価し、改善点を見つけてさらに改良していく「PDCAサイクル(Plan-Do-Check-Action)」を回すことが不可欠です。
PDCAサイクルとは、目標を設定し(Plan)、実行し(Do)、結果を検証し(Check)、改善策を実施する(Action)ことです。
このサイクルを継続的に回すことで、現場の自律的な改善力が高まり、持続的な生産性向上が実現します。
つまり、標準化によって作業の安定性を確保し、PDCAサイクルによって継続的な改善を実現することで、誰もが高い品質で効率的に働ける職場環境が完成するのです。
成功事例:デジタル技術で加速する技術継承
熟練技術者の高齢化と後継者不足は待ったなしの課題です。ここでは、デジタル技術を活用して、課題であった技術継承のプロセスを加速させ、成功した具体的な事例を見ていきましょう。
成功事例① 熟練技術のデータ化・可視化(醸造食品製造業)
長年の経験と勘がものをいう日本酒や醤油などの醸造食品製造業において、熟練の杜氏(とうじ)や職人が持つ発酵の進捗を見極める「目」や「鼻」といった感覚的なノウハウを、センサー技術やAIを活用してデータ化する取り組みが進んでいます。
具体的には、醪(もろみ)の温度、糖度、アルコール度数、香気成分などを各種センサーで常時モニタリングし、そのデータをAIが解析します。熟練者がどのような条件下でどのような判断を下しているのかを学習させ、最適な醸造プロセスを導き出します。
このシステムにより、経験の浅い技術者でも品質の安定した製品づくりが可能になるだけでなく、熟練技術者はより高度な判断や新たな製品開発に注力できるようになりました。
成功事例② 動画マニュアルで実現する技能伝承(機械加工業)
機械加工業においては、複雑な機械操作や精密な加工技術の習得に時間がかかることが一般的です。従来の紙ベースのマニュアルでは伝えきれない細かなコツや注意点を、動画を活用して分かりやすく伝承する企業が増えています。
例えば、熟練技術者が行うNC旋盤の段取り替え作業や、特殊な治具の使い方などを動画で撮影し、ポイントごとにテロップやナレーションで解説を加えます。これにより、若手作業員は自分のペースで繰り返し学習できますし、言葉だけでは理解しにくい「見て覚える」部分を効果的に補うことができます。



最近では、AR(拡張現実)技術を活用し、実際の機械に作業手順を重ねて表示するような、より高度なトレーニングシステムも登場しています。
このように、動画やAR技術を活用した技術伝承により、従来の課題を解決しながら、効率的で質の高い人材育成が可能になります。
成功事例③ AI活用によるノウハウデジタル化(金属加工業)
金属加工の現場では、素材の種類や形状、加工条件によって微妙な調整が求められるなど、熟練者の経験則に頼る部分が多く残っています。AIを活用することで、これらの暗黙知をデジタルデータとして蓄積し、形式知化する試みも始まっています。
具体的には、過去の加工データ(材質、刃物の種類、回転数、送り速度、加工結果など)をAIに学習させ、新たな加工案件に対して最適な加工条件をAIが提案するシステムです。
また、加工中の音や振動をセンサーで検知し、AIが異常を早期に発見したり、工具の摩耗度合いを予測したりすることもでき、不良品の削減や設備の予防保全にも繋がっています。
AIが熟練者の暗黙知をデータ化し、最適化提案から予防保全まで幅広くサポートすることで、金属加工業の生産性と品質が飛躍的に向上する可能性を秘めているわけです。
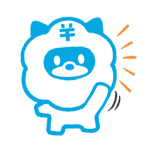
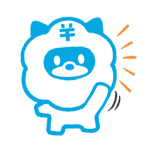
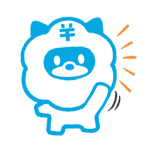
日本電気株式会社(NEC)は、製造業における技術継承の課題に対応するAIソリューションを提供しており、これらも参考になります。
中小製造業が壁を突破した生産性改善事例
デジタル技術の活用は有効ですが、それだけが生産性改善の道ではありません。ここでは、中小製造業が大掛かりなシステム投資だけに頼らず、知恵と工夫で生産性の壁を突破した事例をご紹介します。
事例① AI見積システムで受注率30%向上を実現(樹脂精密加工業)
静岡県の樹脂精密加工業A社(従業員数100名)では、多品種少量の加工がメインで、毎日大量の図面見積りに追われ、回答の遅れが受注機会の損失に繋がっていました。熟練者でないと対応できない見積り業務が属人化し、社内のボトルネックとなっていたのです。
そこで同社が導入したのが、AI見積システム「SellBOT」でした。図面をアップロードするだけでAIが瞬時に見積りを算出し、ワンクリックで回答できるシステムにより、見積り回答スピードが劇的に向上。従来は数日かかっていた見積り回答を最短10分で実現し、日本でトップクラスの回答スピードを達成しました。
この結果、受注率が30%から40%まで大幅にアップ。迅速な対応により顧客満足度も向上し、新規顧客の獲得にも繋がっています。また、ベテラン担当者の負担軽減により、より付加価値の高い業務に集中できるようになったとのことです。
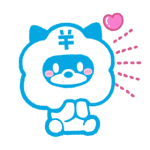
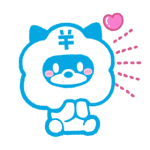
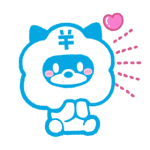
AI技術を活用することで、属人化していた見積り業務を標準化し、スピードと精度の両方を実現した好例ですね。
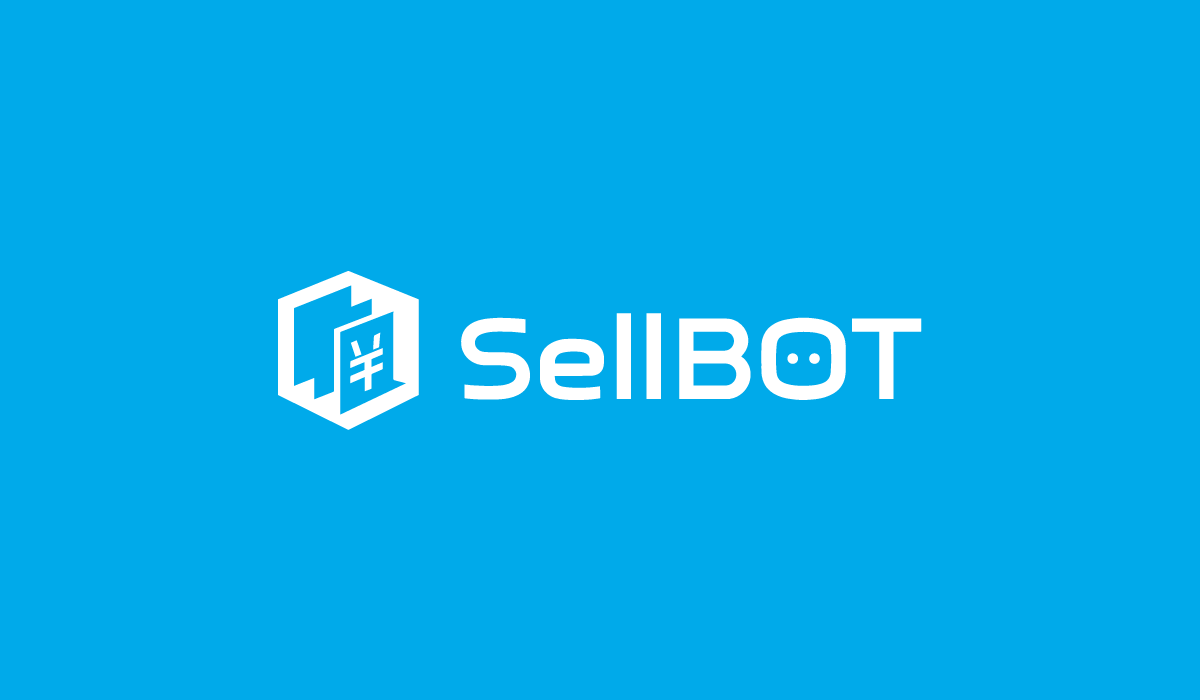
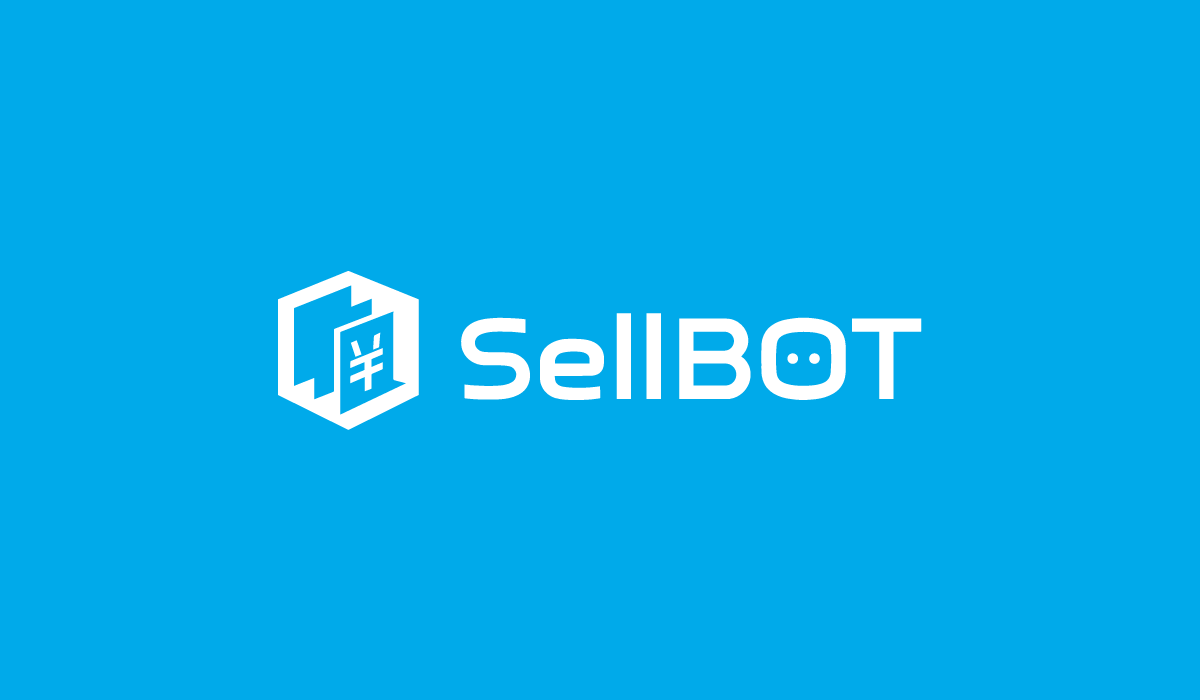
事例② 工場レイアウト最適化(自動車部品メーカー)
ある自動車部品メーカーでは、受注量の増加に伴い工場が手狭になり、モノや人の動線が複雑化していました。
そこで、専門家のアドバイスも受けながら、工場全体のレイアウトを見直すプロジェクトを実施。部品の受け入れから加工、組み立て、検査、出荷までの一連の流れを分析し、工程間の移動距離や滞留時間が最小になるように機械設備や作業台の配置を変更しました。
その結果、モノの移動にかかる時間と労力が大幅に削減され、仕掛品の滞留も減少。リードタイムの短縮と生産能力の向上を実現しました。
大掛かりな設備投資を行わなくても、現状の資源を最大限に活かす工夫で大きな成果を上げた好例と言えるでしょう。



「工場レイアウトの最適化」は、すぐにでも着手できる改善テーマの一つですね。
事例③ IoTセンサーで設備稼働率を向上(金属加工業)
金属加工業においては、NC工作機械などの高価な設備が停止している時間は、そのまま機会損失に繋がります。とある中小企業の金属加工会社では、旧式の機械が多く、故障による突発的な停止や、段取り替えに時間がかかることが課題でした。
そこで、比較的安価に導入できる後付けのIoTセンサーを各設備に取り付け、稼働状況(稼働中、停止中、準備中など)をリアルタイムで「見える化」を実現。これにより、どの設備がいつ、どれくらいの時間停止しているのかが正確に把握できるようになり、停止要因の分析と対策が進みました。
また、個々の機械の稼働データから、予防保全のタイミングを最適化することで、突発的な故障を未然に防ぎ、設備全体の稼働率を大幅に向上させることに成功しました。
このように、低コストなIoT技術の導入により、設備の稼働状況を見える化し、予防保全を最適化することで、中小企業でも大幅な生産性向上を実現できることが実証されました。
事例④ クラウド活用で情報共有を効率化(機械部品メーカー)
複数の営業拠点や工場を持つ機械部品メーカーでは、設計図面や見積書、納期情報などの共有が部門ごと、あるいは個人持ちのファイルで行われており、情報の錯綜や更新漏れが頻発していました。特に、顧客からの急な仕様変更や納期問い合わせへの対応に時間がかかっていたのです。
そこで、クラウドベースの情報共有システムを導入。図面や各種ドキュメントを一元管理し、アクセス権限を設定した上で、どこからでも最新の情報にアクセスできるようにしました。
これにより、営業担当者が出先からでも最新の図面を確認したり、工場側がリアルタイムで生産進捗を共有したりすることが可能になり、部門間の連携がスムーズになりました。
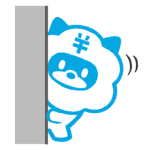
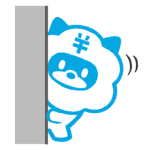
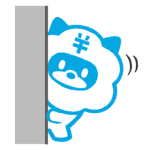
クラウドを導入したことで、意思決定の迅速化、ミスの削減、顧客対応のスピードアップが実現し、間接部門の生産性向上にも大きく貢献したんですね。
製造業DXを成功させる段階的ロードマップ
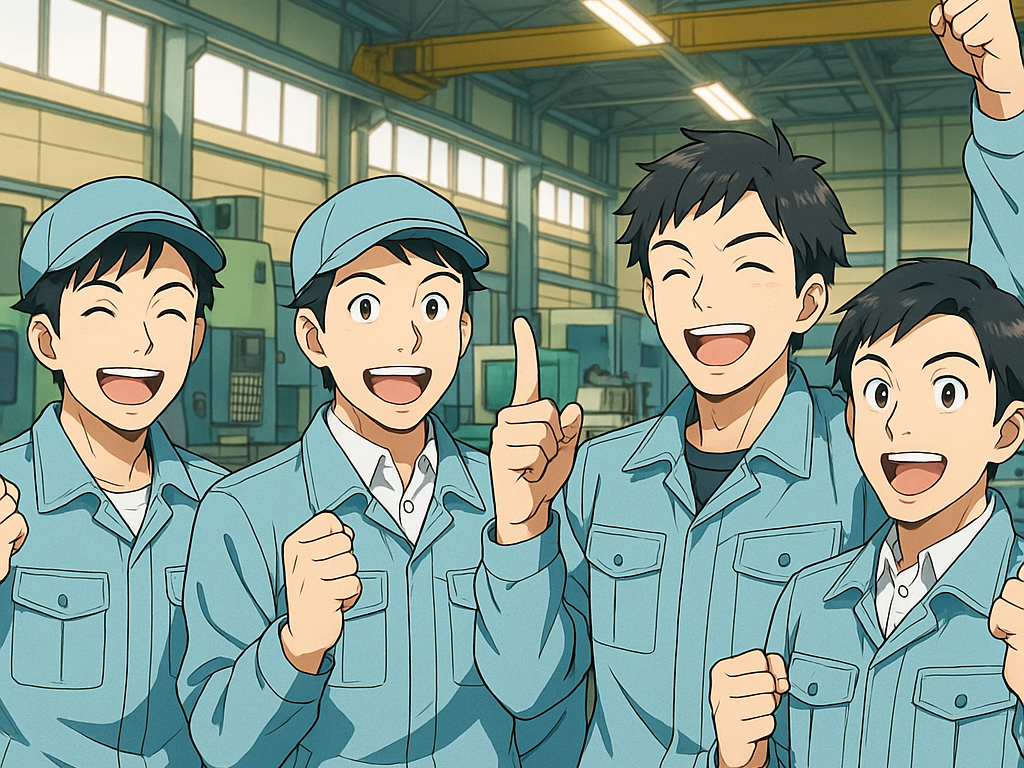
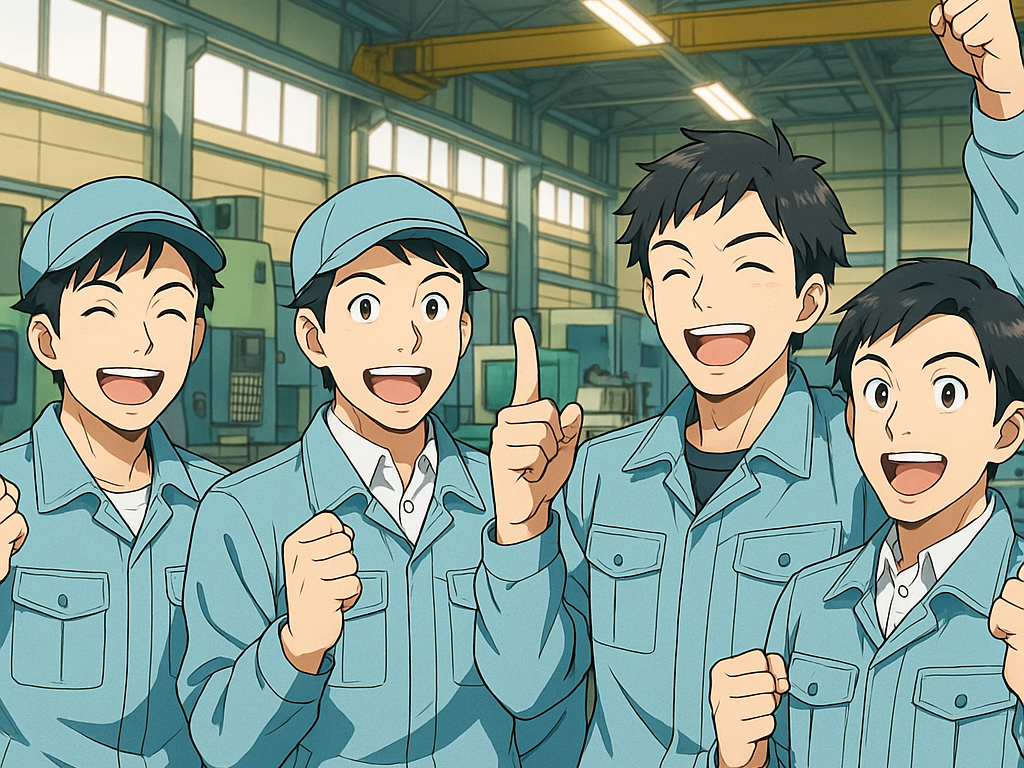
生産性向上と技術継承の課題を解決する強力な手段として期待されるDX(デジタルトランスフォーメーション)ですが、やみくもに最新技術を導入しても成功は望めません。ここでは、中小製造業がDXを成功させるための段階的なロードマップについて解説していきます。
DX視点での課題定義とロードマップ策定
DX推進の第一歩は、自社の経営課題や事業戦略を明確にし、その中でデジタル技術がどのように貢献できるのかを具体的に定義することです。単に「AIを導入したい」「IoTを使いたい」といった技術先行の考え方ではなく、「技術継承のスピードを2倍にする」「不良品率を現在の半分にする」といった具体的な目標を設定し、その達成のためにどのようなデジタル技術が有効かを検討します。
その上で、短期的・中長期的視点から、優先順位をつけてDXの取り組みテーマを洗い出し、具体的な実行計画=ロードマップを策定します。この際、スモールスタートで成果を積み上げながら、段階的に範囲を拡大していくアプローチが、特にリソースの限られる中小製造業には有効です。
このように、明確な目標設定とロードマップに基づいた段階的なアプローチにより、中小製造業でも確実に成果を上げながらDXを推進することができます。
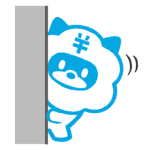
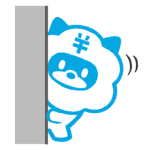
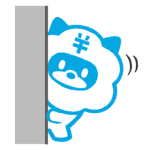
経営層がリーダーシップを発揮し、全社的なコンセンサスを形成しながら進めることが重要です。
現場の理解と参画を引き出す変革マネジメント
DXは単なるツールの導入ではなく、業務プロセスや企業文化そのものの変革を伴います。そのため、現場の従業員の理解と協力なしには成功しません。新しい技術やシステムが導入されることに対する不安や抵抗感を和らげ、むしろ積極的に変革に参加してもらうための「変革マネジメント」が不可欠です。
具体的には、
- DXの目的やメリットを丁寧に説明し、従業員の声に耳を傾けること
- 導入初期には、操作研修の実施とサポート体制の整備
- 小さな成功体験を共有し、モチベーションを高める工夫も大切
- 現場のキーパーソンを巻き込み、DX推進の旗振り役として活躍してもらう
つまり、丁寧なコミュニケーション、適切なサポート、成功体験の共有、現場との連携により、従業員が主体的にDXに取り組む組織文化を築くことが成功の鍵となるのです。
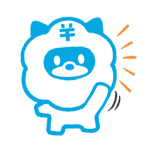
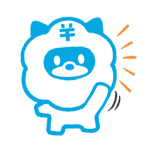
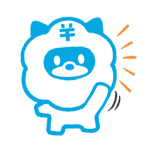
経営層と現場が一体となって取り組む姿勢が、変革を成功に導きます。
投資対効果を最大化するシステム選定のコツ
DX推進にはシステム導入が伴うことが多いですが、その選定は慎重に行う必要があります。高機能で高価なシステムを導入しても、使いこなせなければ意味がありません。自社の規模や業務内容、従業員のITスキルレベルなどを考慮し、本当に必要な機能を見極めることが重要です。
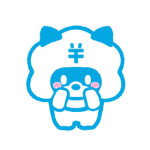
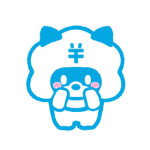
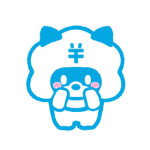
まずは、スモールスタートが可能なクラウドサービスや、既存システムと連携しやすいソリューションを検討するのも良いでしょう。
複数のベンダーから提案を受け、機能だけでなく、導入実績、サポート体制、そして何よりも自社の課題解決に本当に貢献してくれるのかという視点で比較検討します。
また、導入前に無料トライアルやデモンストレーションを積極的に活用し、実際に操作感や機能性を確認することも失敗を防ぐポイントです。
短期的なコストだけでなく、長期的な運用コストや拡張性も考慮し、投資対効果を最大化できるシステムを選びましょう。
まとめ:技術継承と生産性向上を同時に実現する未来戦略
本記事では、中小製造業が直面する生産性向上の課題、特に熟練技術者の高齢化に伴う技術継承の危機を乗り越え、持続的な成長を遂げるためのDX戦略について、具体的な事例やステップを交えながら解説してきました。
日本の製造業を取り巻く環境は厳しさを増していますが、デジタル技術の進化は、これらの課題を解決し、新たな競争力を生み出す大きなチャンスをもたらしています。重要なのは、自社の現状と課題を正しく認識し、背伸びをせず、着実なステップで改善を進めていくことです。
アナログな改善活動で土台を固めつつ、効果的なデジタル技術を選定し、現場の理解と協力を得ながらDXを推進することで、技術継承と生産性向上という二つの大きなテーマを同時に実現することは決して不可能ではありません。
本記事が、貴社の未来戦略を考える上での一助となれば幸いです。
製造業の技術継承・生産性向上に関するQ&A
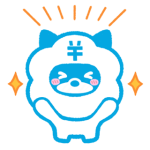
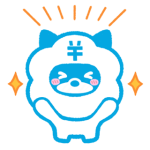
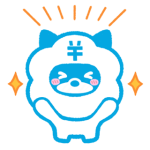
これらの疑問を解決するためには、まず自社の現状分析から始め、段階的に取り組みを進めることが重要です。
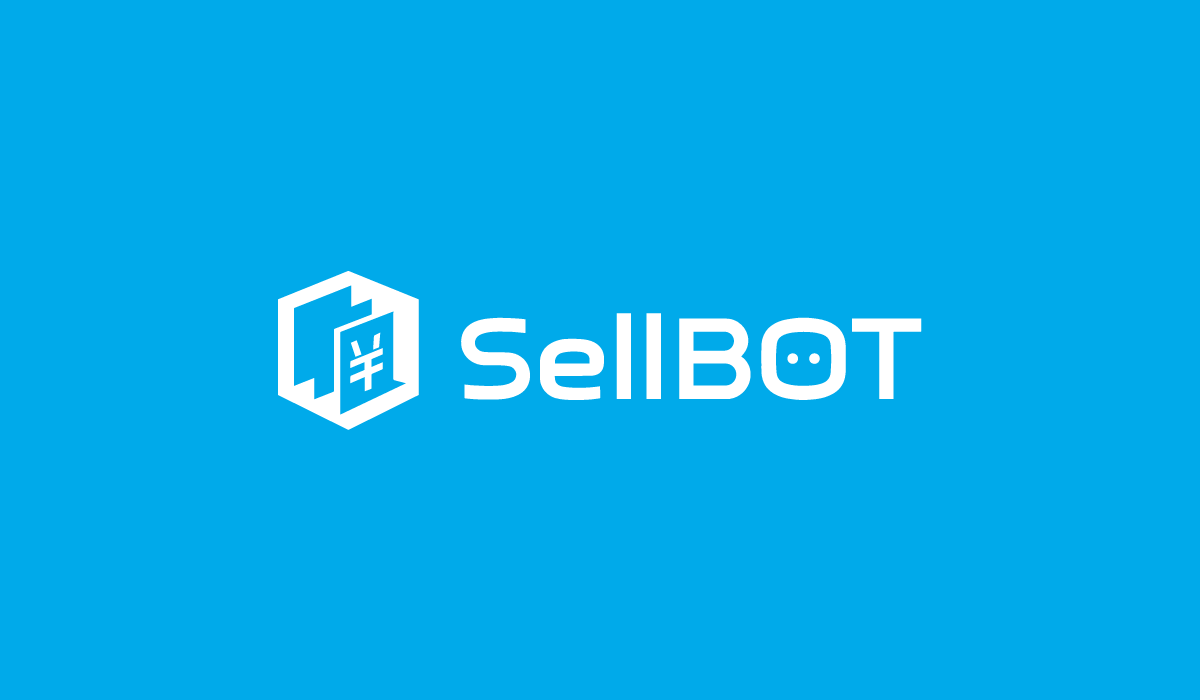
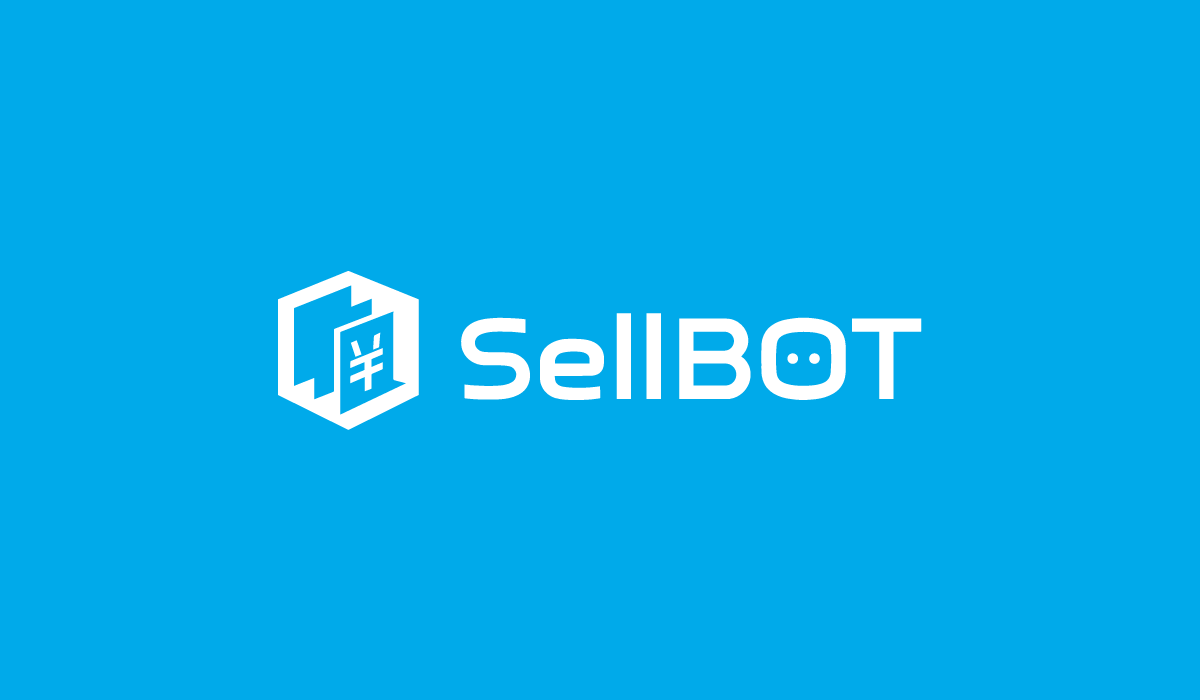