製造業における発注業務の現状と課題
製造業において発注業務は、製品の品質やコスト、納期に直結する重要な業務プロセスです。しかし、多くの企業ではいまだに手作業やアナログな方法で発注業務を行っており、様々な非効率や問題が生じています。これらの課題を解決することは、製造業のDX(デジタルトランスフォーメーション)において重要な一歩となります。
手作業による発注業務の問題点
データ入力ミスと再作業の発生
手作業による発注業務の最も大きな問題点の一つは、データ入力ミスの発生とそれに伴う再作業です。発注担当者が手動でシステムに情報を入力する際、数量や品番、納期などの情報を誤って入力してしまうことは珍しくありません。例えば、「100個」と発注すべきところを「10個」と入力してしまったり、似た品番を取り違えたりするケースが頻繁に発生しています。
このようなミスが発生すると、単に修正するだけでなく、関連する業務にも影響が波及します。誤った発注情報に基づいて生産計画が立てられ、資材が不足して生産ラインが止まってしまったり、逆に過剰な在庫を抱えることになったりするのです。また、取引先とのやり取りで混乱が生じ、信頼関係にも影響を与えかねません。
あるケースでは、製造業A社が手作業で行っていた発注業務において、月平均で約5%の発注書に何らかのミスが含まれており、それらを修正するために発注担当者の業務時間の約15%が費やされていたという調査結果もあります。これは単なる時間の無駄だけでなく、担当者の心理的負担にもなり、さらなるミスを誘発する悪循環を生み出していました。
さらに、入力ミスによる再作業は、単純に二度手間になるだけでなく、緊急対応を要することも多く、通常業務の流れを乱し、他の重要な業務にも影響を及ぼします。発注ミスを修正するために電話やメールでの確認作業が増え、本来なら他の価値創造的な業務に充てるべき時間が失われているのです。
担当者への過度な依存と属人化
発注業務が手作業中心であると、特定の担当者の経験やノウハウに依存する「属人化」が進みがちです。長年発注業務を担当してきたベテラン社員は、取引先との関係性や過去の取引履歴、価格交渉のコツなど、形式化されていない暗黙知を多く持っています。こうした知識は非常に価値がある一方で、その担当者が不在になったり退職したりした場合、業務の継続性に大きなリスクをもたらします。
例えば、ある中堅製造業では、20年以上発注業務を担当していたベテラン社員が突然の病気で長期休暇を取ることになった際、代わりの担当者が業務を引き継いだものの、取引先との特別な契約条件や価格交渉の経緯などの情報が十分に文書化されておらず、通常の1.5倍の時間をかけても業務が回らない状況に陥りました。結果として、納期遅延や不適切な発注条件での取引が発生し、数百万円の損失が生じたケースもあります。
また、属人化は業務の標準化や改善を妨げる要因にもなります。「自分のやり方が一番効率的」と考えるベテラン担当者は、新しいシステムやプロセスの導入に抵抗を示すことがあります。これにより、全社的な業務効率化やデジタル化の取り組みが停滞してしまうのです。
さらに、属人化された業務環境では、知識やスキルの共有が進まず、組織全体の成長が阻害されます。新しい担当者の育成にも時間がかかり、人材の流動性や柔軟な人員配置が難しくなるという問題も生じます。
紙・Excel管理の限界
多くの製造業では、発注業務においていまだに紙の発注書やExcelファイルによる管理が主流となっています。これらの方法は導入コストが低く、使い慣れているという利点がありますが、業務の拡大や複雑化に伴い、様々な限界が露呈しています。
紙ベースの発注管理では、書類の紛失や破損のリスクがあるほか、保管スペースの確保も課題となります。また、過去の発注履歴を検索する際も、大量の書類から必要な情報を探し出す手間がかかります。あるアンケート調査では、紙ベースで発注管理を行っている企業の担当者は、情報検索に週あたり平均4時間以上を費やしているという結果も出ています。
Excelによる管理も、一見便利なように思えますが、ファイルの共有や更新に関する問題が付きまといます。複数の担当者が同じファイルを編集すると、バージョン管理が複雑になり、最新の情報がどれなのか分からなくなることがあります。また、Excelファイルが増えていくと、どのファイルに何の情報が入っているのかを把握するのも一苦労です。
さらに、紙やExcelでは、発注データと他のシステム(例えば会計システムや在庫管理システム)との連携が困難であり、同じデータを複数のシステムに手動で入力する必要が生じます。これは単に非効率なだけでなく、システム間でのデータの不整合を引き起こす原因にもなります。
ある製造業B社では、Excelで管理していた発注データと会計システムのデータに不整合が生じ、月次決算の際に大幅な修正作業が必要となり、財務部門の残業時間が増加する事態となりました。また、重要な発注情報を含むExcelファイルが誤って削除され、バックアップからの復旧に丸一日を要したケースもあります。
このように、紙やExcelによる発注管理は、小規模な業務では機能するものの、業務の拡大や複雑化に伴い、情報の検索性、共有性、整合性、安全性などの面で深刻な限界を露呈します。
発注業務の非効率がもたらす影響
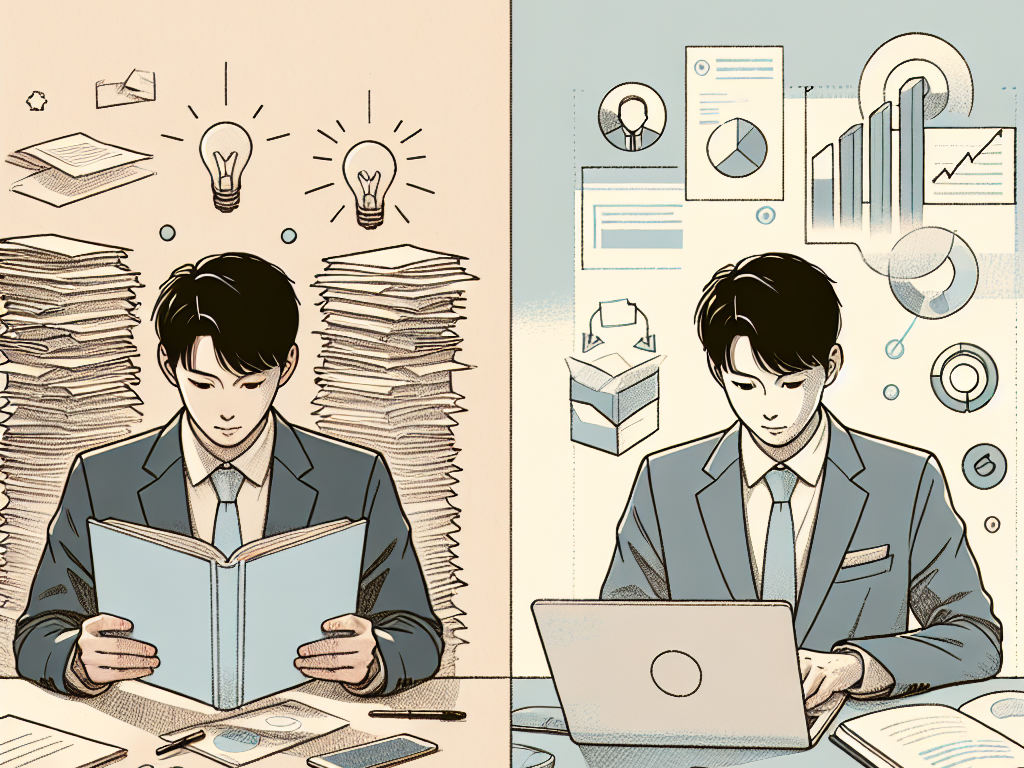
コスト増加と利益率の低下
発注業務の非効率は、直接的・間接的に様々なコスト増加を引き起こし、最終的には企業の利益率低下につながります。まず、手作業による発注処理には多くの人的リソースが必要となります。発注書の作成、承認プロセス、取引先とのやり取り、データ入力など、一連の作業に多くの時間が費やされています。
製造業の調査によると、非効率な発注プロセスを持つ企業では、発注1件あたりの処理コストが効率的なプロセスを持つ企業の2〜3倍になるというデータもあります。例えば、効率的な企業では発注1件あたりの処理コストが500〜1,000円程度であるのに対し、非効率な企業では1,500〜3,000円かかっているケースも少なくありません。
また、発注ミスによる緊急対応や特急発注は、通常より高いコストを支払うことになります。例えば、通常の納期では1個あたり1,000円の部品が、緊急発注では1,500円になるといったケースは珍しくありません。緊急輸送費や残業代なども加わり、コストは雪だるま式に増加します。
在庫管理の非効率も大きな問題です。発注タイミングを誤ると、過剰在庫による保管コストの増加や、逆に在庫不足による生産ラインの停止といったリスクが生じます。ある製造業では、発注管理の非効率により年間在庫コストが約15%増加していたという事例もあります。
これらのコスト増加は最終的に製品の原価に反映され、企業の利益率を押し下げる要因となります。製造業の平均的な営業利益率が5〜10%程度であることを考えると、発注業務の非効率による数パーセントのコスト増加は、利益に大きな影響を与えかねません。
納期遅延とサプライチェーンへの影響
発注業務の非効率は、納期遅延という形で顕在化し、サプライチェーン全体に波及的な影響を及ぼします。発注の遅れや誤りは、原材料や部品の調達遅延を引き起こし、それが生産計画の変更や生産ラインの停止につながることがあります。
ある自動車部品メーカーでは、発注担当者の入力ミスにより特定の部品の発注が遅れ、生産ラインが半日停止する事態が発生しました。この停止により、約500万円の機会損失が生じただけでなく、納期遅延により顧客である自動車メーカーの生産計画にも影響を与え、取引関係の悪化につながりました。
納期遅延は、直接的な損失だけでなく、顧客満足度の低下や企業評価の悪化といった長期的な影響ももたらします。特に自動車や電子機器などのジャストインタイム方式を採用している業界では、部品の納期遅延は即座に生産ラインの停止につながるため、サプライヤーの評価において納期遵守率は非常に重要な指標となっています。
また、納期遅延は自社だけでなく、サプライチェーン全体に連鎖的な影響を及ぼします。一次サプライヤーの納期遅延は、二次、三次のサプライヤーにも影響し、最終的には市場への製品投入遅延につながることもあります。特にグローバルなサプライチェーンを持つ企業では、この連鎖的な影響はより複雑で深刻なものとなります。
さらに、納期遅延を回避するために安全在庫を増やすという対応は、在庫コストの増加を招き、資金効率の悪化につながります。このように、発注業務の非効率は、単なる社内の問題ではなく、サプライチェーン全体の効率性と競争力に影響を与える重要な課題なのです。
従業員の負担増と業務品質の低下
発注業務の非効率は、担当者の業務負担を増大させ、結果として業務品質の低下を招きます。手作業による発注処理、データの二重入力、ミスの修正作業などにより、発注担当者は本来の戦略的な業務に集中できなくなっています。
ある中堅製造業の調査では、発注担当者の業務時間の内訳を分析したところ、約60%が単純なデータ入力や書類作成、約20%がミスの修正や問い合わせ対応に費やされており、サプライヤー関係の強化や調達戦略の検討といった付加価値の高い業務にはわずか20%程度しか時間を割けていないことが明らかになりました。
この状況は、担当者のモチベーション低下や燃え尽き症候群(バーンアウト)のリスクを高めます。単調で付加価値の低い作業が大半を占める環境では、仕事の満足度が低下し、離職率の上昇につながる可能性があります。実際、非効率な業務プロセスを持つ企業では、効率的なプロセスを持つ企業と比較して、従業員の離職率が15〜20%高いというデータもあります。
また、業務負担の増大は、注意力の低下やミスの増加といった形で業務品質に直接影響します。長時間の単調な作業を続けると、人間の集中力は低下し、ミスを見逃しやすくなります。ある研究によれば、8時間以上連続して同じ作業を行うと、ミスの発生率が通常の2倍以上になるというデータもあります。
さらに、過度の業務負担はワークライフバランスの悪化を招き、従業員の健康問題や長期的な生産性低下につながる恐れもあります。特に月末や期末など、発注業務が集中する時期には残業が常態化し、担当者の心身の健康に悪影響を及ぼすケースも少なくありません。
このように、発注業務の非効率は、単に業務処理の遅延やコスト増加だけでなく、人的資源の最適活用を妨げ、組織全体の活力と創造性を低下させる要因となっているのです。
発注業務効率化のメリットと導入効果
発注業務の効率化は、単なるコスト削減や時間短縮にとどまらず、企業全体の競争力強化につながる重要な取り組みです。適切なシステムやプロセスを導入することで得られるメリットは多岐にわたります。
業務時間とコストの削減
処理時間の短縮と工数削減
発注業務の効率化によってもたらされる最も直接的なメリットは、処理時間の短縮と工数削減です。従来の手作業による発注プロセスでは、発注書の作成、承認取得、発注データの入力、発注状況の確認など、多くの手順が必要でした。これらの作業を自動化またはシステム化することで、大幅な時間短縮が可能になります。
例えば、ある自動車部品メーカーでは、発注システムを導入することで、発注処理時間が従来の約1/3に短縮されました。具体的には、1件あたりの発注処理に平均15分かかっていたものが、システム導入後は5分程度で完了するようになったのです。この会社では月間約2,000件の発注を行っていたため、単純計算で月あたり約333時間(約42人日)の工数削減に成功しました。
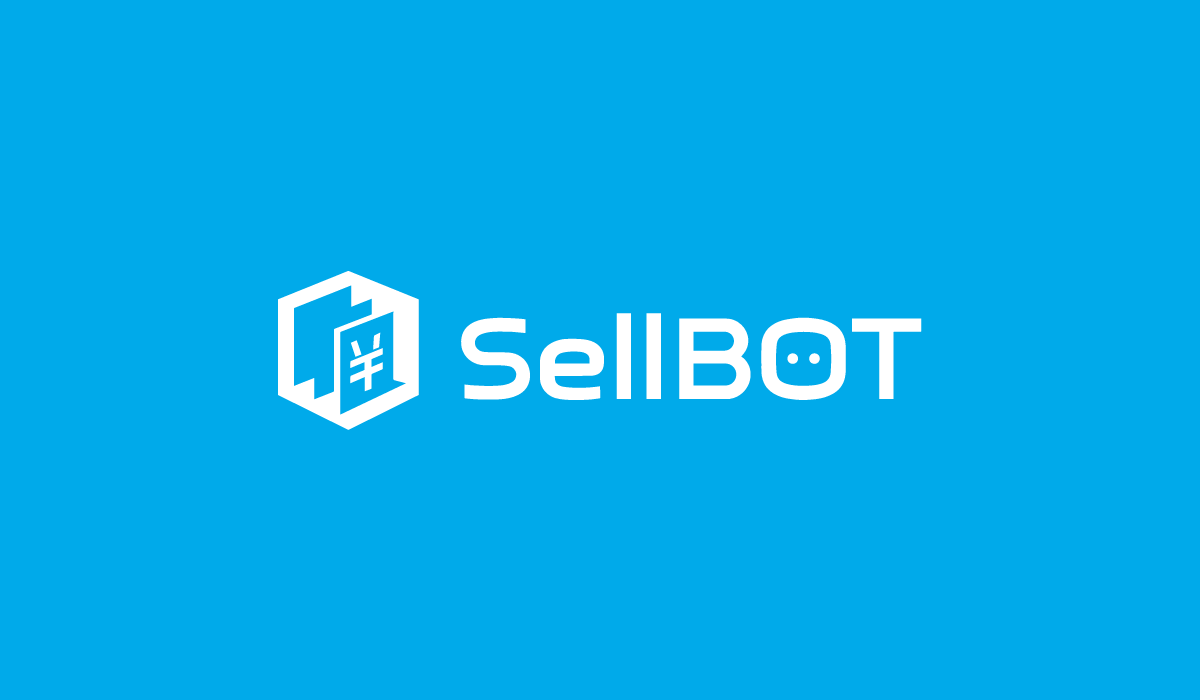
また、発注プロセスの自動化により、承認フローもスムーズになります。
従来は紙の発注書を持ち回りで承認を得ていたプロセスが、システム上で電子的に完結するようになり、承認者の不在による遅延が解消されました。ある電子部品メーカーでは、承認プロセスの電子化により、承認にかかる時間が平均2日から4時間に短縮されたという事例もあります。
さらに、定期発注や反復発注の自動化も大きな効果をもたらします。
定期的に発注する標準部品や原材料については、あらかじめ設定した条件に基づいて自動発注するシステムを導入することで、担当者の作業負担を大幅に軽減できます。ある製造業では、全発注の約60%を占める定期発注を自動化することで、発注担当者の業務時間を約40%削減することに成功しました。
このような処理時間の短縮と工数削減は、単に業務効率を高めるだけでなく、発注担当者がより戦略的な業務(サプライヤー関係の強化、新規調達先の開拓、コスト削減交渉など)に集中できる環境を作り出します。ある調査によれば、発注業務を効率化した企業では、調達担当者が戦略的業務に費やす時間が平均で40%増加したというデータもあります。
人件費と間接コストの最適化
発注業務の効率化は、人件費と間接コストの最適化にも大きく貢献します。
処理時間の短縮と工数削減により、同じ人員でより多くの発注処理が可能になるため、人員増加を抑制しながら事業拡大に対応できるようになります。
ある中堅製造業では、受注増加に伴い発注業務の負担が増大していましたが、発注システムの導入により、追加人員を雇用することなく業務量の増加に対応することができました。この会社では、システム導入前の予測では2名の増員が必要と試算されていましたが、効率化により増員を回避できたため、年間約1,000万円の人件費削減効果があったと報告しています。
また、発注ミスの減少による間接コストの削減効果も見逃せません。
手作業による発注では、数量や品番の入力ミス、納期設定の誤りなどが発生しやすく、これらのミスを修正するための追加作業や緊急対応が必要になります。システム化により入力ミスを防止することで、これらの追加コストを削減できます。
ある電機メーカーでは、発注システム導入前は月平均で全発注の約3%にミスが含まれており、その修正に月間約40時間の追加作業が発生していました。システム導入後はミス率が0.5%未満に減少し、修正作業も月間約5時間程度にまで削減されました。
さらに、発注業務の効率化は、残業時間の削減にもつながります。特に月末や期末など業務が集中する時期には、発注担当者の残業が常態化している企業も少なくありません。システム化により処理が効率化されれば、こうした残業時間を削減できます。ある製造業では、発注システム導入により発注部門の月間残業時間が平均30%減少し、年間約300万円の残業手当削減につながったという事例もあります。
また、業務効率化により空いた時間を他の価値創造的な業務に充てることで、人的リソースの有効活用が可能になります。コスト削減交渉やサプライヤー評価、市場調査など、より戦略的な業務に時間を割くことで、調達コストの削減や調達品質の向上といった二次的な効果も期待できます。
ペーパーレス化によるコスト削減
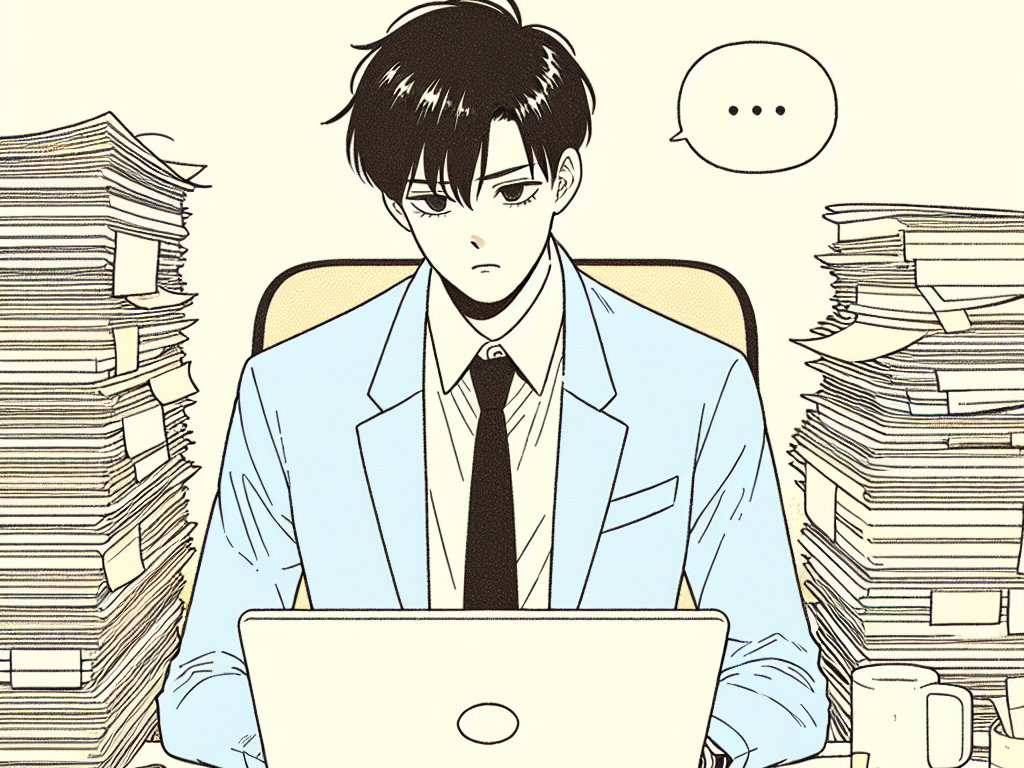
発注業務のシステム化に伴うペーパーレス化は、直接的なコスト削減効果をもたらします。従来の紙ベースの発注プロセスでは、発注書、納品書、検収書、請求書など、多くの書類が発生し、その印刷・保管・管理にコストがかかっていました。
ある中堅製造業では、月間約3,000件の発注に対し、1件あたり平均3枚の書類(発注書、納品書のコピー、検収書など)が発生していました。これは月間約9,000枚、年間では約108,000枚の紙が使用されていたことになります。発注システムの導入により、これらの書類を電子化することで、年間の用紙代、印刷費、ファイリング用品費などで約100万円のコスト削減を実現しました。
また、紙の書類を保管するためのスペースコストも無視できません。書類保管用のキャビネットやバインダー、保管室などのスペースは、オフィスの賃料という形で企業にコスト負担をもたらしています。ある調査によれば、一般的なオフィスでは、書類保管スペースがオフィス面積の約15〜20%を占めているとされています。
ある電子機器メーカーでは、発注関連書類のデジタル化により、書類保管用のキャビネット20台分のスペースが不要になりました。このスペースを会議室や作業スペースに転用することで、オフィスの有効活用が可能になったほか、新たなオフィススペースの賃借を回避できたため、年間約300万円の賃料削減効果があったと報告しています。
さらに、紙の書類検索や整理にかかる時間コストの削減も重要です。紙ベースの管理では、過去の発注履歴や取引条件を確認するために、大量の書類から必要な情報を探し出す必要がありました。電子化により、キーワード検索や条件検索が可能になり、情報へのアクセス時間が大幅に短縮されます。
ある製造業の調査では、紙ベースの管理では過去の発注情報を探すのに平均10分かかっていたのが、システム導入後は30秒程度に短縮されました。月間約100回の検索が行われていたとすると、月あたり約16時間の時間削減効果があったことになります。
また、ペーパーレス化は環境負荷の低減にも貢献します。紙の使用量削減によるCO2排出削減効果は、企業のESG(環境・社会・ガバナンス)評価にもプラスの影響を与えます。ある大手製造業では、発注業務のペーパーレス化により年間約5トンのCO2排出削減効果があったと試算し、環境報告書で公表しています。
データ精度と業務品質の向上
入力ミスと転記ミスの防止
発注業務の効率化において、データ精度の向上は非常に重要なメリットの一つです。従来の手作業による発注プロセスでは、品番や数量の入力ミス、納期の設定ミスなど、人為的なエラーが発生しやすい環境にありました。これらのミスは、単に修正作業が必要になるだけでなく、在庫過剰や欠品、生産ラインの停止など、深刻な問題を引き起こす可能性があります。
システム化された発注プロセスでは、様々な機能によりこうした入力ミスや転記ミスを防止することができます。例えば、バーコードやQRコードによるデータ読み取り、プルダウンメニューからの選択入力、入力値の範囲チェック、必須項目の入力漏れ防止など、多層的なエラー防止機能を実装することが可能です。
ある自動車部品メーカーでは、発注システム導入前は月平均で約4%の発注に何らかのミスが含まれていましたが、システム導入後はこれが0.5%未満に減少しました。特に効果が大きかったのは、類似品番の誤入力防止機能と数量の妥当性チェック機能で、これらにより従来最も多かったミスの約80%が解消されたと報告しています。
また、複数システム間でのデータ転記も大きなミスの原因となっていました。例えば、生産管理システムから必要数量を確認し、それを手作業で発注システムに入力するといったプロセスでは、転記ミスが発生しやすくなります。システム間の自動連携を実現することで、こうした転記ミスを完全に排除することができます。
ある電子機器メーカーでは、生産計画システム、在庫管理システム、発注システムを連携させることで、必要数量の自動計算と発注データへの自動反映を実現しました。これにより、従来発生していた転記ミスがゼロになっただけでなく、発注処理時間も約70%短縮されたと報告しています。
さらに、発注データの入力時に過去の取引実績や標準価格との乖離をチェックする機能を実装することで、異常値の早期発見も可能になります。例えば、通常1個100円の部品を1,000円で発注してしまうようなミスを、入力時点で警告表示することで防止できます。
ある製造業では、このような価格チェック機能により、年間約500万円相当の過剰支払いを未然に防止できたと試算しています。また、数量の妥当性チェック(例:通常の10倍の数量が入力された場合に警告を表示する)により、過剰発注による在庫増加リスクも大幅に低減されました。
このように、発注業務のシステム化によるデータ精度の向上は、単にミスを減らすだけでなく、それに伴う様々な二次的問題(過剰在庫、欠品、緊急対応、取引先との信頼関係悪化など)を防止する効果があり、企業全体の業務品質向上に大きく貢献します。
データの一元管理と可視化
発注業務の効率化において、データの一元管理と可視化は非常に重要なメリットです。従来の分散管理(紙の書類、個人のExcelファイル、メールなど)では、最新の情報がどこにあるのか分からなくなったり、情報の整合性が取れなくなったりするリスクがありました。
システム化により発注データを一元管理することで、常に最新かつ正確な情報にアクセスできるようになります。例えば、発注状況、納期、価格履歴、取引先情報などを統合的に管理し、必要な時に必要な形で取り出せるようになります。
ある機械メーカーでは、従来は発注担当者ごとに異なるExcelファイルで発注情報を管理していたため、全社の発注状況を把握するには各担当者のファイルを集めて集計する必要がありました。発注システムの導入により、リアルタイムで全社の発注状況を把握できるようになり、月次の発注実績レポート作成に要する時間が従来の3日から半日に短縮されました。
また、データの一元管理により、様々な切り口での分析が可能になります。例えば、取引先別の発注金額、品目別の価格推移、納期遵守率など、多角的な分析が容易になります。これにより、コスト削減の機会や取引先の評価、調達戦略の策定などに役立つ洞察を得ることができます。
ある電子部品メーカーでは、発注データの一元管理により、取引先別の価格分析を実施したところ、同じ仕様の部品でも取引先によって最大30%の価格差があることが判明しました。この分析結果を基に価格交渉を行い、年間約2,000万円のコスト削減を実現しました。
さらに、データの可視化はダッシュボードやレポーティング機能を通じて、経営層や関連部門への情報提供を効率化します。例えば、発注金額の推移、主要取引先との取引状況、納期遅延の発生状況などを視覚的に表示することで、迅速な意思決定をサポートします。
ある製造業では、発注システムから得られるデータを基に、月次の調達会議用のダッシュボードを自動生成する仕組みを構築しました。これにより、会議準備の工数が大幅に削減されただけでなく、データに基づいた議論が活性化し、より効果的な調達戦略の立案につながったと報告しています。
また、データの一元管理は監査対応や内部統制の強化にも貢献します。システム上で全ての取引履歴が記録され、承認プロセスも電子的に管理されるため、「いつ、誰が、何を、どのような条件で発注したか」を明確に追跡できるようになります。
ある大手製造業では、内部監査における発注プロセスの検証が、システム導入前は約1週間かかっていたものが、導入後は1日で完了するようになりました。また、不適切な発注(例:承認なしの発注、予算超過の発注など)を未然に防止する仕組みにより、コンプライアンスリスクも大幅に低減されました。
リアルタイム情報共有の実現
発注業務の効率化において、リアルタイムでの情報共有は非常に重要なメリットです。従来の紙やExcelベースの発注管理では、最新の発注状況や納期情報を関係者間で共有するには、メールや会議、電話などの手段が必要でした。これらの方法では情報の伝達に時間がかかり、また情報が古くなるリスクもありました。
システム化により、発注情報をリアルタイムで共有できるようになると、関連部門(生産管理、在庫管理、経理など)が常に最新の情報にアクセスできるようになります。これにより、情報の伝達遅れによる問題(生産計画の遅延、在庫の過不足など)を防止できます。
ある自動車部品メーカーでは、発注システムの導入により、発注情報が生産管理システムにリアルタイムで連携されるようになりました。これにより、納期変更があった場合に即座に生産計画に反映できるようになり、生産ラインの停止リスクが大幅に低減されました。同社の報告によれば、システム導入前は月平均2〜3回発生していた「部品未着による生産調整」が、導入後はほぼゼロになったとのことです。
また、リアルタイム情報共有は、問い合わせ対応の効率化にも貢献します。従来は「この部品はいつ納入されるのか」「この発注の承認状況はどうなっているのか」といった問い合わせに対し、発注担当者が個別に調査して回答する必要がありました。システム化により、こうした情報を関係者が自ら確認できるようになり、問い合わせ対応の負担が軽減されます。
ある電機メーカーでは、発注システムのポータル機能により、関連部門が発注状況を自ら確認できるようになった結果、発注担当者への問い合わせが月平均約100件から20件程度に減少しました。これにより、発注担当者は本来の業務に集中できるようになり、生産性が向上したと報告しています。
さらに、取引先とのリアルタイム情報共有も重要です。Webポータルやクラウドシステムを活用することで、発注情報を取引先と直接共有し、納期回答や出荷通知などの情報をオンラインで受け取ることができます。これにより、電話やFAXでのやり取りが削減され、コミュニケーションの効率化と正確性向上が実現します。
ある機械部品メーカーでは、主要取引先20社と連携する発注ポータルを構築し、発注情報の共有と納期回答のオンライン化を実現しました。これにより、発注から納期回答までの平均リードタイムが3日から1日に短縮され、また納期遵守率も85%から95%に向上したと報告しています。
また、リアルタイム情報共有は、テレワークやリモートワークの環境下でも業務の継続性を確保する上で重要な役割を果たします。クラウドベースの発注システムであれば、場所を選ばず最新の情報にアクセスでき、承認作業なども遠隔で行うことができます。
ある製造業では、コロナ禍でのテレワーク導入時に、クラウド型の発注システムが大きな効果を発揮しました。発注担当者が在宅勤務でも通常通り業務を継続でき、承認者も外出先からモバイルアプリで承認作業を行うことができたため、業務の停滞を最小限に抑えることができたと報告しています。
戦略的な意思決定の支援
調達データの分析と活用
発注業務の効率化がもたらす重要なメリットの一つは、蓄積された調達データを分析し、戦略的な意思決定に活用できるようになることです。従来の紙ベースやExcelの分散管理では、データの収集と集計に多大な労力がかかり、タイムリーな分析が困難でした。
システム化により、全ての発注データが構造化された形で蓄積されるため、様々な切り口での分析が容易になります。例えば、調達コストの推移、取引先別の発注金額、品目別の価格変動、季節変動など、多角的な分析が可能になります。
ある電子機器メーカーでは、発注システムから得られるデータを活用して、主要原材料の価格推移と市場価格の相関分析を行いました。その結果、特定の取引先からの調達価格が市場価格の変動に連動していないことが判明し、価格交渉の材料として活用することで年間約3,000万円のコスト削減を実現しました。
また、発注データと他のデータ(例:品質データ、生産データ)を組み合わせることで、より高度な分析も可能になります。例えば、調達コストと製品品質の関係性分析、取引先ごとの納入品質の比較、コスト削減施策の効果測定などが挙げられます。
ある自動車部品メーカーでは、発注データと品質データを統合分析することで、低価格の部品を調達した場合の不良率上昇と、それに伴う追加コスト(検査工数増、返品処理、生産ライン停止など)を定量化しました。この分析結果を基に、「表面的な調達コスト」ではなく「総所有コスト(TCO)」の観点から最適な調達先を選定する方針に変更し、結果として年間の品質コストを約20%削減することに成功しました。
さらに、AIや機械学習を活用した高度な分析も可能になります。例えば、過去の発注パターンから需要予測を行い、最適な発注タイミングと数量を提案するシステムや、異常な発注パターンを検出して不正や誤りを防止するシステムなどが実現可能です。
ある製造業では、発注データと販売データを組み合わせたAI需要予測システムを導入し、発注量の最適化を図りました。その結果、在庫水準を約15%削減しながらも、欠品率を5%から1%未満に改善することに成功しました。これにより、年間約1億円の在庫削減効果と、約5,000万円の機会損失削減効果が得られたと報告しています。
また、調達データの分析は、サプライチェーンリスクの可視化にも役立ちます。例えば、特定の取引先や地域への依存度が高い部品を特定し、リスク分散策を講じることができます。
ある電子機器メーカーでは、2011年の東日本大震災後、調達データを分析して「単一調達先に依存している部品」を特定し、代替調達先の開拓を進めました。その後の2016年熊本地震では、この取り組みにより部品調達の停滞を最小限に抑え、生産への影響を大幅に軽減できたと報告しています。
このように、発注業務のシステム化によって蓄積される調達データは、単なる業務記録ではなく、戦略的な意思決定を支援する貴重な経営資源となります。データ分析に基づく調達戦略の立案と実行は、コスト削減、リスク管理、品質向上など、多方面での競争力強化につながります。
サプライヤー評価の高度化
発注業務の効率化により、サプライヤー評価を高度化し、より戦略的なサプライヤー管理が可能になります。従来の断片的な情報に基づく主観的な評価から、データに基づく客観的で多面的な評価へと進化させることができます。
システム化された発注プロセスでは、納期遵守率、品質不良率、価格競争力、対応スピードなど、サプライヤーのパフォーマンスに関するデータが自動的に蓄積されます。これらのデータを活用して、サプライヤーを定量的に評価し、比較することが可能になります。
ある自動車部品メーカーでは、発注システムから得られるデータを基に、主要サプライヤー50社について「納期」「品質」「価格」「対応力」「技術力」の5項目を定量評価するスコアカードを自動生成する仕組みを構築しました。これにより、四半期ごとのサプライヤー評価会議の準備工数が従来の1/5に削減されただけでなく、客観的なデータに基づく建設的な議論が可能になり、サプライヤー管理の質が向上したと報告しています。
また、サプライヤー評価の結果を取引先と共有し、改善を促す取り組みも効果的です。評価結果をポータルサイトなどで共有することで、取引先の自発的な改善活動を促進できます。
ある電機メーカーでは、サプライヤーポータルを通じて月次の評価結果(納期遵守率、品質不良率など)を取引先と共有する仕組みを導入しました。これにより、取引先の改善意識が高まり、導入から1年で全体の納期遵守率が85%から95%に、品質不良率が1.2%から0.6%に改善されたと報告しています。
さらに、高度なサプライヤー評価は、戦略的な取引先選定や発注配分の最適化にも活用できます。例えば、評価結果に基づいて取引先をランク分けし、高評価の取引先への発注比率を高めるといった施策が可能になります。
ある製造業では、サプライヤー評価システムを導入し、評価結果に基づいて取引先を4段階(S/A/B/C)にランク分けしました。その上で、Sランクの取引先への発注比率を高め、Cランクの取引先との取引を段階的に縮小する方針を採用しました。この結果、2年間で納期遅延による生産調整が約70%減少し、調達品質も大幅に向上したと報告しています。
また、サプライヤー評価データは、新規取引先の開拓や既存取引先との価格交渉においても有効活用できます。客観的なデータに基づく評価結果は、交渉の強力な裏付けとなります。
ある機械メーカーでは、サプライヤー評価データを活用した価格交渉を実施し、「同等の品質・納期パフォーマンスを持つ他社はこの価格で供給している」といった具体的なデータを示すことで、主要取引先との価格交渉を有利に進め、平均3%の価格削減を実現しました。
さらに、サプライヤー評価は、サプライチェーンリスクの管理にも役立ちます。例えば、財務状況が不安定な取引先や、品質問題が頻発する取引先を早期に特定し、リスク対策を講じることができます。
ある電子部品メーカーでは、サプライヤー評価システムに「リスク指標」を追加し、納期遅延の頻度増加や品質不良の増加傾向を検出する仕組みを導入しました。これにより、ある取引先の経営悪化の兆候をいち早く察知し、代替調達先の確保を進めたことで、その後の取引先の倒産時にも部品調達への影響を最小限に抑えることができたと報告しています。
在庫最適化と資金効率の改善
発注業務の効率化は、在庫の最適化と資金効率の改善に大きく貢献します。適切な発注タイミングと数量の決定は、過剰在庫や欠品を防ぎ、在庫回転率の向上と資金効率の改善につながります。
システム化された発注プロセスでは、在庫状況、需要予測、リードタイムなどのデータを統合的に分析し、最適な発注点と発注量を算出することが可能になります。例えば、経済的発注量(EOQ)モデルや定期発注方式、かんばん方式など、様々な在庫管理手法をシステム上で実装できます。
ある電子部品メーカーでは、発注システムと在庫管理システムを連携させ、品目ごとの需要変動パターンとリードタイムを考慮した自動発注の仕組みを導入しました。これにより、在庫水準を約20%削減しながらも、欠品率を従来の3%から0.5%に低減することに成功しました。この在庫削減効果は、年間約1.5億円の運転資金削減に相当すると試算されています。
また、発注業務の効率化により、リードタイム短縮も実現できます。発注から納品までの時間が短縮されれば、安全在庫を減らすことが可能になります。
ある自動車部品メーカーでは、発注システムの導入と取引先との情報連携強化により、平均調達リードタイムを10日から6日に短縮することに成功しました。これにより、安全在庫を約30%削減し、年間約2億円の在庫削減効果を得たと報告しています。
さらに、発注データと販売データを連携させることで、需要の変動に応じた動的な発注調整も可能になります。例えば、販売が好調な製品の部品は発注量を増やし、販売が鈍化している製品の部品は発注を抑制するといった柔軟な対応が可能になります。
ある家電メーカーでは、POSデータと発注システムを連携させ、販売動向に応じて週次で発注計画を自動調整する仕組みを導入しました。これにより、季節商品の在庫過剰や欠品を大幅に削減し、在庫回転率を1.2回転/月から1.8回転/月に向上させることに成功しました。この改善により、年間約3億円の運転資金削減効果があったと試算されています。
また、発注業務の効率化は、支払条件の最適化にも寄与します。発注データと請求データを適切に管理することで、支払いのタイミングを最適化し、キャッシュフローを改善することができます。
ある製造業では、発注システムと会計システムの連携により、支払予定を正確に把握し、早期支払割引の活用や支払いタイミングの最適化を図りました。これにより、年間約2,000万円の割引メリットを享受しながらも、平均支払日数を適切に管理し、キャッシュフローの改善を実現したと報告しています。
さらに、発注データの分析により、ABC分析(重要度による分類)やFSN分析(回転率による分類)などの手法を活用した在庫管理の高度化も可能になります。これにより、品目ごとに最適な発注・在庫管理方針を適用できます。
ある機械メーカーでは、発注システムから得られるデータを基にABC×FSN分析を実施し、品目ごとに最適な発注方針(自動発注/定期発注/都度発注など)と在庫水準を設定しました。この結果、全体の在庫金額を約15%削減しながらも、重要部品の欠品率を大幅に低減することに成功したと報告しています。
このように、発注業務の効率化は、単に発注プロセスの改善にとどまらず、在庫最適化による資金効率の改善、キャッシュフローの改善など、財務面での大きなメリットをもたらします。これらの改善は、企業の収益性向上と財務体質強化に直接貢献します。
発注業務効率化のためのシステム選定
発注業務を効率化するためには、自社の業務特性や規模に合ったシステムを選定することが重要です。最適なシステム選定は、導入効果を最大化し、投資対効果(ROI)を高める鍵となります。
自社に最適なシステムの選び方
業務規模と予算に合わせたシステム選定
発注システムを選定する際には、自社の業務規模と予算に合わせた適切な選択が重要です。過剰な機能を持つ高価なシステムを導入しても、その機能を十分に活用できなければ投資効果は限定的になります。逆に、将来の成長を見据えずに小規模なシステムを選ぶと、すぐに限界に達してしまう可能性があります。
まず、発注業務の規模を定量的に把握することが重要です。例えば、月間発注件数、取引先数、品目数、発注金額、関連部門数などの指標を整理しましょう。これらの指標に基づいて、必要なシステム規模を見積もることができます。
ある中堅製造業では、月間発注件数約1,000件、取引先数約100社、品目数約5,000点という業務規模を考慮し、中規模の発注システムを選定しました。当初は大手ベンダーの大規模システムも検討していましたが、機能の多くが使われない可能性が高く、コストパフォーマンスが低いと判断したのです。結果として、必要十分な機能を持つ中規模システムを選択したことで、予算内での導入を実現し、高いROIを達成できたと報告しています。
予算については、初期導入コストだけでなく、ランニングコスト(保守料、ライセンス料など)も含めた総所有コスト(TCO)で考える必要があります。クラウド型システムは初期投資が抑えられる一方、長期的には月額料金の累積でコストが大きくなる可能性があります。オンプレミス型は初期投資が大きい反面、長期利用ではランニングコストが抑えられるケースもあります。
ある電子部品メーカーでは、5年間のTCOを試算した結果、クラウド型とオンプレミス型でほぼ同等のコストとなりました。そこで、初期投資の負担軽減と迅速な導入を優先し、クラウド型を選択しました。この判断により、予算の平準化と早期の効果創出を実現できたと報告しています。
また、業務規模の成長予測も重要な考慮点です。今後数年間で発注件数や取引先数が大幅に増加する見込みがある場合は、スケーラビリティ(拡張性)の高いシステムを選ぶべきでしょう。
ある成長中の製造業では、今後3年間で事業規模が2倍になる計画があったため、初期段階では過剰と思われる規模のシステムを選定しました。これにより、事業拡大に伴うシステム再構築の手間とコストを回避でき、結果的に総コストの削減につながったと報告しています。
さらに、段階的な導入アプローチも検討価値があります。最初は基本的な発注機能のみを導入し、その効果を確認しながら徐々に機能を拡張していく方法です。これにより、初期投資を抑えつつ、確実に効果を出しながら発展させていくことができます。
ある中小製造業では、最初は発注書作成と承認プロセスの電子化のみを実施し、その後、取引先ポータル、在庫連携、分析機能などを段階的に追加していきました。この方法により、各段階での効果を確認しながら投資を進められたため、経営層の継続的な支持を得やすく、結果として5年計画を予定通り完遂できたと報告しています。
このように、業務規模と予算に合わせたシステム選定は、投資効果を最大化し、持続可能な発注業務の効率化を実現するための基盤となります。過大投資や過小投資を避け、自社に最適なシステムを選ぶことが成功の鍵です。
クラウド型とオンプレミス型の比較
発注システムを導入する際の重要な選択肢として、クラウド型とオンプレミス型があります。それぞれに特徴とメリット・デメリットがあり、自社の状況や優先事項に合わせて選択する必要があります。
クラウド型発注システムは、インターネットを通じてサービスとして提供されるシステムで、SaaS(Software as a Service)とも呼ばれます。初期投資が少なく、短期間で導入できるのが大きな特徴です。また、サーバーやソフトウェアの保守・管理はベンダーが行うため、自社のIT部門の負担が軽減されます。
ある中堅製造業では、IT部門の人員が限られていたため、システム運用の負担を最小化できるクラウド型を選択しました。導入から2ヶ月で本稼働を開始でき、IT部門は戦略的なプロジェクトに集中できるようになったと報告しています。
クラウド型のもう一つのメリットは、定期的なアップデートにより常に最新機能を利用できる点です。ベンダーが継続的に機能改善や法改正対応を行うため、システムの陳腐化を心配する必要がありません。
ある電子部品メーカーでは、クラウド型発注システムを採用したことで、インボイス制度対応や電子帳簿保存法の改正対応などを特別な追加投資なく実現できたと報告しています。オンプレミス型であれば、これらの対応のためにシステム改修が必要だったと試算しています。
一方、クラウド型のデメリットとしては、カスタマイズの自由度が限られる点が挙げられます。多くのクラウドサービスは標準機能のパラメータ設定による調整は可能ですが、コアな機能を大幅に変更することは難しい場合が多いです。
ある製造業では、独自の承認フローや特殊な発注形態があったため、クラウド型では対応が難しいと判断し、カスタマイズ性の高いオンプレミス型を選択しました。これにより、自社の業務プロセスに完全に適合したシステムを構築できたと報告しています。
オンプレミス型発注システムは、自社のサーバーにソフトウェアをインストールして運用するタイプです。初期投資は大きくなりますが、長期利用ではコスト面で有利になる場合があります。また、自社の要件に合わせた細かいカスタマイズが可能な点が大きなメリットです。
ある大手製造業では、複雑な承認フローや特殊な発注形態に対応するため、オンプレミス型を選択し、自社の業務プロセスに完全に適合したシステムを構築しました。初期投資は大きかったものの、10年以上の長期利用を前提とした場合のTCOはクラウド型より低くなると試算されています。
オンプレミス型のもう一つのメリットは、データセキュリティやコンプライアンス面での安心感です。特に機密性の高い発注情報を扱う企業や、規制の厳しい業界では、自社でデータを管理できるオンプレミス型が選ばれることがあります。
ある防衛関連の製造業では、セキュリティポリシーの観点から、発注データを社外に置くことができないと判断し、オンプレミス型を選択しました。これにより、厳格なセキュリティ要件を満たしつつ、発注業務の効率化を実現できたと報告しています。
一方、オンプレミス型のデメリットとしては、システムの保守・運用負担が大きい点が挙げられます。サーバーの管理、バックアップ、セキュリティ対策、バージョンアップなど、継続的な運用管理が必要となります。
ある製造業では、オンプレミス型の発注システムを導入したものの、IT部門のリソース不足により適切な保守・運用ができず、システムの不具合や性能劣化が頻発する事態に陥りました。結果として、3年後にクラウド型へ移行する決断をしたと報告しています。
近年は、これらの中間的な選択肢として、プライベートクラウドやハイブリッド型も増えています。これらは、クラウドの利便性とオンプレミスのセキュリティや制御性を両立させる方法として注目されています。
選択にあたっては、コスト(初期/運用)、カスタマイズ性、セキュリティ要件、IT部門の体制、導入スピードなど、多角的な観点から自社に最適な形態を検討することが重要です。
必要機能のリストアップと優先順位付け
発注システムを選定する際には、必要な機能を明確にリストアップし、優先順位を付けることが重要です。全ての要望を満たすシステムを見つけることは難しいため、「必須機能」と「あれば便利な機能」を区別し、優先度の高い機能から順に検討していくアプローチが効果的です。
まず、発注業務の流れを詳細に分析し、各ステップで必要となる機能を洗い出します。一般的な発注システムの主要機能としては、以下のようなものが挙げられます。
- 発注書作成・管理機能
- 承認ワークフロー機能
- 取引先管理機能
- 品目マスタ管理機能
- 価格管理機能
- 納期管理・追跡機能
- 受入・検収機能
- 予算管理・チェック機能
- レポーティング・分析機能
- 外部システム連携機能
これらの機能について、自社にとっての重要度を「必須」「重要」「あれば便利」などの段階で評価します。この評価には、現場の発注担当者だけでなく、関連部門(経理、生産管理、品質管理など)の意見も取り入れることが重要です。
ある機械メーカーでは、システム選定にあたり、発注部門、経理部門、生産管理部門、IT部門からメンバーを集めたワーキンググループを結成し、各部門の視点から必要機能とその優先度を整理しました。この過程で、当初は見落としていた「為替レートの自動反映機能」や「図面ファイルの添付機能」などの重要要件が追加され、結果として各部門のニーズを満たすシステム選定につながったと報告しています。
また、現在の課題を解決する機能を優先することも重要です。例えば、現状で納期管理に最も問題を抱えているなら、納期追跡機能を重視するといった具合です。
ある電子部品メーカーでは、発注業務の最大の課題が「承認プロセスの遅延」だったため、モバイル承認機能や代理承認機能、承認期限アラート機能などの承認ワークフロー関連機能を最優先要件としてシステム選定を行いました。その結果、承認プロセスの平均所要時間が3日から0.5日に短縮され、最大の課題を効果的に解決できたと報告しています。
さらに、将来の拡張性も考慮することが重要です。現時点では必要ないが、将来的に必要になる可能性が高い機能についても検討しておくべきです。
ある製造業では、当初はシンプルな発注管理のみを想定していましたが、将来的なグローバル展開を見据えて、多言語・多通貨対応や国際取引向けの機能(インコタームズ対応、輸出入書類作成など)にも対応可能なシステムを選定しました。2年後に海外拠点が増えた際、追加開発なしでスムーズに対応できたと報告しています。
機能の優先順位付けにあたっては、コスト対効果の観点も重要です。一部の高度な機能は追加コストが高い場合があるため、その機能がもたらす効果と追加コストのバランスを考慮する必要があります。
ある中小製造業では、AI需要予測機能に魅力を感じていましたが、追加コストが高額だったため、費用対効果を検討した結果、現段階では基本的な発注管理機能を優先し、AI機能は将来のオプションとして検討することにしました。これにより、限られた予算内で最大の効果を得られるシステム構成を実現できたと報告しています。
最終的に、機能要件をまとめた「要件定義書」を作成し、複数のベンダーやシステムを比較評価するための基準とします。各システムが自社の要件をどの程度満たしているかを定量的に評価することで、客観的な選定が可能になります。
ある電機メーカーでは、約100項目の機能要件リストを作成し、各項目の重要度(1〜5点)と各システムの対応レベル(0〜3点)をスコアリングして総合評価を行いました。この方法により、感覚的な判断ではなく、定量的な評価に基づいてシステムを選定することができたと報告しています。
既存システムとの連携ポイント
ERPや生産管理システムとの統合
発注システムの効果を最大化するためには、既存のERP(統合基幹業務システム)や生産管理システムとの適切な連携が不可欠です。システム間の連携がスムーズでないと、データの二重入力や不整合が発生し、効率化のメリットが大幅に減少してしまいます。
ERPシステムとの連携では、マスタデータ(取引先情報、品目情報、価格情報など)の共有と、トランザクションデータ(発注データ、受入データ、支払データなど)の連携が主な焦点となります。理想的には、マスタデータはERPを主体として一元管理し、発注システムはそれを参照する形が望ましいでしょう。
ある自動車部品メーカーでは、SAPをERPとして使用しており、発注システム導入時に最も重視したのがSAPとの連携でした。取引先マスタと品目マスタはSAPで一元管理し、発注システムはリアルタイムでこれらのマスタを参照する仕組みを構築しました。これにより、マスタ管理の二重化を回避し、データ整合性を確保することに成功したと報告しています。
トランザクションデータについては、発注システムで作成された発注データをERPに連携し、会計処理(債務計上、支払処理など)に活用する流れが一般的です。また、ERPで管理されている予算情報や原価情報を発注システムに連携し、予算チェックや原価管理に活用するケースもあります。
ある電機メーカーでは、発注システムとERPの連携により、発注時に予算チェックを自動化し、予算超過の発注を事前に防止する仕組みを構築しました。これにより、従来は月次決算時に発覚していた予算超過問題を未然に防ぐことができ、予算管理の精度が大幅に向上したと報告しています。
生産管理システムとの連携も重要です。生産計画から算出される資材所要量を発注システムに連携し、適切なタイミングで必要量を発注する仕組みを構築することで、在庫の最適化が可能になります。
ある機械メーカーでは、MRP(資材所要量計画)システムと発注システムを連携させ、生産計画の変更が自動的に発注計画に反映される仕組みを構築しました。これにより、生産計画変更に伴う発注調整の手間が大幅に削減され、また計画変更への対応遅れによる過剰在庫や欠品のリスクも低減されたと報告しています。
システム統合にあたっては、リアルタイム連携とバッチ連携のどちらが適切かを業務要件に応じて検討する必要があります。例えば、発注承認時に予算チェックを行う場合はリアルタイム連携が必要ですが、日次の集計データ連携であればバッチ処理で十分な場合もあります。
ある製造業では、マスタデータは日次バッチで連携し、予算チェックはリアルタイム連携、発注データは承認完了時に即時連携という形で、データの種類と業務要件に応じて最適な連携方式を選択しました。これにより、システム負荷を抑えつつ、必要な箇所ではリアルタイム性を確保するバランスの取れた連携を実現したと報告しています。
また、既存システムのバージョンや技術的制約も考慮する必要があります。特に古いERPシステムとの連携では、インターフェース開発に追加コストがかかる場合があります。
APIによるシームレスな連携
近年の発注システムでは、API(Application Programming Interface)を活用したシームレスな連携が重要なポイントとなっています。APIは異なるシステム間でデータやコマンドをやり取りするための標準的な仕組みであり、柔軟で効率的なシステム連携を実現します。
API連携の大きなメリットは、リアルタイムでのデータ交換が可能になることです。例えば、発注システムから在庫管理システムのリアルタイム在庫数を照会したり、会計システムの予算残高をチェックしたりといった連携が可能になります。
ある電子部品メーカーでは、発注システムと在庫管理システムをAPI連携することで、発注入力時に最新の在庫状況を確認できる仕組みを構築しました。これにより、在庫情報の古さによる誤発注を防止し、適正在庫の維持に成功したと報告しています。
また、API連携はシステム間の疎結合を実現し、一方のシステム変更が他方に与える影響を最小化できるメリットもあります。従来の密結合型の連携では、一方のシステムの変更が他方のシステムに大きな影響を与え、改修コストが高くなりがちでした。
ある製造業では、ERPシステムのバージョンアップ時に、API連携を採用していたおかげで発注システム側の改修が最小限で済み、予定よりも短期間・低コストでバージョンアップを完了できたと報告しています。
さらに、API連携はクラウドサービスとの統合を容易にします。多くのクラウドサービスはAPIを公開しており、これを活用することで様々なサービスと連携できます。
ある機械メーカーでは、発注システムとクラウド型のサプライヤー評価システムをAPI連携し、発注実績データを自動的に評価システムに送信する仕組みを構築しました。これにより、従来は手動で行っていたデータ転記作業が不要になり、評価作業の効率が大幅に向上したと報告しています。
API連携を検討する際は、以下のポイントに注意することが重要です。
まず、セキュリティ対策です。APIはシステム間の「入口」となるため、適切な認証・認可の仕組みや通信の暗号化が必要です。
ある大手製造業では、API連携のセキュリティ強化のため、OAuth 2.0による認証、API呼び出し制限、通信の暗号化、アクセスログの監視などの対策を実施しました。これにより、セキュアな連携を実現しつつ、システム間の柔軟なデータ連携を可能にしたと報告しています。
次に、エラー処理とリカバリーの仕組みです。API連携はネットワーク障害やシステム障害により一時的に失敗する可能性があるため、適切なエラー処理とリトライの仕組みが必要です。
ある電機メーカーでは、API連携のエラー発生時に自動的にリトライする仕組みと、一定回数失敗した場合に管理者に通知する仕組みを実装しました。これにより、一時的な障害による連携失敗を最小限に抑え、重大な問題が発生した場合には迅速に対応できる体制を整えたと報告しています。
また、API連携のパフォーマンスも重要な検討点です。大量のデータをリアルタイムで連携する場合、システムに負荷がかかる可能性があります。
ある製造業では、発注データのAPI連携において、当初はすべての項目をリアルタイム連携していましたが、システム負荷が高くなったため、必須項目のみをリアルタイム連携し、詳細情報はバッチ処理で連携する方式に変更しました。これにより、システム負荷を適正化しつつ、業務に必要なリアルタイム性を確保することに成功したと報告しています。
データ移行と互換性の確保
新しい発注システムを導入する際、既存システムからのデータ移行と互換性の確保は非常に重要なポイントです。適切なデータ移行計画がないと、過去の重要な発注履歴や取引条件などの情報が失われたり、新旧システム間でデータの不整合が生じたりする恐れがあります。
データ移行を成功させるためには、まず移行対象データの範囲と優先順位を明確にする必要があります。一般的には、マスタデータ(取引先情報、品目情報、価格マスタなど)が最も重要で、次いで未完了の進行中取引データ(発注済み・未納品の発注書など)、そして過去の取引履歴という順になります。
ある電子部品メーカーでは、データ移行にあたり、「全取引先マスタと直近2年間の取引がある取引先の価格履歴」「現在進行中の全発注データ」「直近1年間の完了済み発注履歴」という優先順位を設定しました。これにより、限られた移行期間内で最も重要なデータを確実に移行することができたと報告しています。
また、データ移行前のクレンジング(データ浄化)も重要です。長年使用してきた旧システムには、重複データや不整合データ、未使用のマスタなどが蓄積されている場合が多いです。これらをそのまま新システムに移行すると、新システムでも同じ問題を抱えることになります。
ある機械メーカーでは、新システム導入を機に、取引先マスタのクレンジングを実施しました。その結果、約20%が重複または未使用のマスタであることが判明し、これらを整理した上で移行を行いました。これにより、新システムでのマスタ管理が効率化され、ユーザーの検索性も向上したと報告しています。
データ形式の変換も重要な課題です。旧システムと新システムでは、データ構造やコード体系が異なる場合が多く、適切な変換ルールを定義する必要があります。
ある製造業では、旧システムと新システムで品目コードの体系が異なっていたため、変換テーブルを作成して対応しました。また、移行期間中は両方のコードを併記する運用とし、ユーザーの混乱を最小限に抑える工夫を行ったと報告しています。
さらに、データ移行のテストと検証も欠かせません。実際の移行前に、テスト環境でサンプルデータを使った移行テストを繰り返し実施し、問題点を洗い出して対策を講じることが重要です。
ある電機メーカーでは、本番移行の3ヶ月前から毎週データ移行テストを実施し、その都度発見された問題点を修正していきました。本番移行直前には、実データの10%を使った大規模テストも行い、移行プロセスの信頼性を高めたことで、本番移行はほぼ計画通りに完了したと報告しています。
移行後の検証も重要です。移行が完了した後、サンプリング検査や集計値の比較などを通じて、データが正しく移行されたことを確認する必要があります。
ある自動車部品メーカーでは、データ移行後に「旧システムと新システムの発注金額の月次集計値比較」「無作為に選んだ100件の発注データの詳細比較」「全取引先の登録情報サンプリング検査」などを実施し、移行の正確性を検証しました。いくつかの不一致が発見され、個別に修正することで、データの整合性を確保できたと報告しています。
また、移行期間中の並行運用計画も重要です。システム切り替え時に業務が停滞しないよう、適切な移行戦略を立てる必要があります。
ある製造業では、週末に移行作業を行い、月曜日から新システムでの運用を開始する計画を立てました。また、移行直後の2週間は旧システムも参照可能な状態を維持し、必要に応じて過去データを確認できるようにしました。これにより、業務の連続性を確保しつつ、スムーズな移行を実現できたと報告しています。
さらに、移行後のフォローアップ体制も重要です。移行直後は予期せぬ問題が発生する可能性が高いため、迅速に対応できる体制を整えておく必要があります。
ある中堅製造業では、システム移行後の1ヶ月間は「発注システム移行サポートデスク」を設置し、ユーザーからの問い合わせや報告に即座に対応できる体制を整えました。また、毎日の終業時にその日の問題と対応策を共有するミーティングを実施し、問題の早期解決と蓄積を防いだと報告しています。
システム導入のコストと投資対効果
初期コストとランニングコストの見積り
発注システム導入を検討する際、適切なコスト見積りは経営判断の重要な基盤となります。コストは大きく分けて「初期コスト」と「ランニングコスト」に分類でき、それぞれを詳細に検討することが重要です。
初期コストには、システム本体の導入費用だけでなく、カスタマイズ費用、データ移行費用、インフラ整備費用、教育・トレーニング費用などが含まれます。特に注意すべきは、表面上の導入費用だけでなく、これらの「隠れたコスト」も含めて総合的に見積もることです。
ある電子部品メーカーでは、発注システム導入時に、システム本体費用は予算内に収まったものの、データ移行の複雑さを過小評価していたため、移行コストが当初見積もりの3倍になってしまいました。結果として総コストが予算を大幅に超過し、他のIT投資計画の見直しを余儀なくされたと報告しています。
カスタマイズについては、必要最小限に抑えることがコスト管理の鍵となります。過剰なカスタマイズは初期コストを押し上げるだけでなく、将来のバージョンアップ時の追加コストにもつながります。
ある機械メーカーでは、当初多数のカスタマイズを検討していましたが、コストと将来の保守性を考慮し、業務プロセスの方をシステムに合わせる方針に変更しました。結果として、カスタマイズ費用を当初見積もりの30%に抑えることができ、また標準機能の範囲内での運用となったことで、その後のバージョンアップも比較的スムーズに行えたと報告しています。
ランニングコストには、システム保守料、ライセンス料、サポート費用、インフラ運用コスト(サーバー、ネットワークなど)、内部運用コスト(システム管理者の人件費など)が含まれます。クラウド型の場合は月額・年額のサブスクリプション料金が主要なコストとなります。
ある製造業では、オンプレミス型とクラウド型の両方を検討し、5年間のTCO(総所有コスト)を比較しました。初期コストはオンプレミス型が高かったものの、ユーザー数の多さからクラウド型の月額料金の累積額が大きくなり、5年間トータルではオンプレミス型の方がコスト優位と判断しました。一方で、キャッシュフローの観点からは初期投資の少ないクラウド型に魅力を感じ、最終的には経営戦略との整合性から判断したと報告しています。
また、システム規模の適正化もコスト管理の重要なポイントです。過大な機能や過剰なライセンスは無駄なコストにつながります。
ある中堅製造業では、当初全社員分のライセンスを検討していましたが、実際にシステムを日常的に使用するユーザー数を精査した結果、必要なライセンス数を60%削減できることが分かりました。これにより、年間のライセンスコストを大幅に削減できたと報告しています。
さらに、隠れたコストとして見落としがちなのが、システム導入に伴う業務停滞や生産性低下のコストです。特に移行期間中や導入直後は、ユーザーの習熟不足や想定外の問題により、一時的に業務効率が低下することがあります。
ある電機メーカーでは、システム導入による一時的な生産性低下を見込んで、導入直後の1ヶ月間は通常の20%増しの人員配置を計画しました。これにより、業務の遅延を防ぎつつ、スムーズな移行を実現できたと報告しています。
コスト見積りの精度を高めるためには、類似規模の他社事例を参考にすることも有効です。業界団体や同業他社との情報交換、コンサルタントの知見活用などを通じて、より現実的な見積りを行うことが可能になります。
ある製造業では、同業他社3社のシステム導入事例を調査し、自社の見積りと比較検証しました。その結果、データ移行コストを過小評価していることが判明し、見積りを修正したことで、より現実的な予算計画を立てることができたと報告しています。
また、コスト削減策として、段階的導入やスコープの最適化も検討価値があります。全機能を一度に導入するのではなく、最も効果の高い機能から順に導入していく方法です。
ある中小製造業では、予算制約から全機能の一括導入が難しかったため、最初は発注書作成・管理機能のみを導入し、その後、効果を確認しながら承認ワークフロー、取引先ポータル、分析機能と段階的に拡張していく計画を立てました。この方法により、各段階で投資対効果を確認しながら進められたため、経営層の継続的な支持を得やすく、結果として5年計画を予定通り完遂できたと報告しています。
ROI計算の方法と評価基準
発注システムへの投資を正当化し、経営層の承認を得るためには、適切なROI(投資対効果)の計算と評価が不可欠です。ROIは単なる数字の計算ではなく、投資判断の重要な材料となります。
ROI計算の基本は、システム導入によって得られる「効果(ベネフィット)」を「投資額(コスト)」で割ることで算出されます。ただし、効果の定量化が難しい場合も多いため、定量的効果と定性的効果の両面から評価することが重要です。
定量的効果としては、主に以下のような項目が挙げられます:
- 人件費削減効果
発注業務の効率化による工数削減 - 在庫削減効果
適正在庫管理による在庫金額の減少 - 調達コスト削減効果
価格分析や交渉力強化による購買コスト低減 - エラー削減効果
発注ミスの減少による再作業や緊急対応コストの削減 - ペーパーレス効果
紙、印刷、保管コストの削減
ある電子部品メーカーでは、発注システム導入のROI計算において、年間の発注件数(約24,000件)に1件あたりの工数削減効果(15分→5分、つまり10分/件の削減)を掛け合わせ、さらに時間単価を乗じることで、年間約800万円の人件費削減効果を算出しました。同様に、発注ミス率の低下(4%→0.5%)による再作業削減効果、在庫削減効果(15%減)、ペーパーレス効果などを合計し、年間約2,000万円の効果を見込みました。5年間で約1億円の効果に対し、5年間のTCOが6,000万円であったため、ROIは約1.67(67%のリターン)と算出され、投資判断の根拠となったと報告しています。
定性的効果としては、以下のような項目が考えられます:
- 業務品質の向上:正確性と一貫性の改善
- 意思決定の迅速化:リアルタイムデータ活用による判断スピード向上
- コンプライアンス強化:承認プロセスの徹底と監査対応の向上
- 従業員満足度向上:単調作業削減によるモチベーション向上
- 取引先との関係強化:情報共有の円滑化と信頼関係の構築
これらの定性的効果は数値化が難しいものの、中長期的な競争力に大きく影響するため、適切に評価することが重要です。
ある機械メーカーでは、定性的効果を「非常に高い」「高い」「中程度」「低い」の4段階で評価し、それぞれに点数(4点、3点、2点、1点)を付けて、定量的効果と合わせた総合評価を行いました。この方法により、直接的なコスト削減効果は小さいものの、業務品質向上やコンプライアンス強化などの定性的効果が高いプロジェクトの価値を適切に評価できたと報告しています。
ROI計算にあたっては、効果の発現時期も考慮する必要があります。システム導入直後から最大効果が得られるわけではなく、ユーザーの習熟や業務プロセスの最適化に伴って、徐々に効果が高まっていくのが一般的です。
ある製造業では、発注システムのROI計算において、1年目は期待効果の50%、2年目は80%、3年目以降は100%という段階的な効果発現を想定しました。これにより、短期的な効果を過大評価せず、より現実的な投資判断が可能になったと報告しています。
また、リスク要因を考慮したシナリオ分析も有効です。「楽観的シナリオ」「標準シナリオ」「悲観的シナリオ」の3つを設定し、それぞれのROIを計算することで、投資の不確実性を評価できます。
ある電機メーカーでは、発注システム導入のROI計算において、標準シナリオでは5年間のROIが1.5、悲観的シナリオ(効果が30%減少、コストが20%増加)でも1.05となることを確認し、リスクを考慮しても投資価値があると判断したと報告しています。
ROIの評価基準については、企業によって異なりますが、一般的には以下のような基準が用いられます:
- 最低必要ROI:多くの企業では、IT投資に対して1.0以上(つまり投資額を上回るリターン)を最低条件としています。
- 期待ROI:競合する投資案件との比較や、過去の類似プロジェクトの実績などを考慮して設定されます。製造業のIT投資では、3年〜5年で1.5〜2.0程度のROIを期待する企業が多いようです。
- 投資回収期間:ROIとは別に、投資額を回収するまでの期間も重要な指標です。多くの企業では2〜3年以内の回収を目標としています。
ある自動車部品メーカーでは、全てのIT投資案件に対して「3年以内に投資回収、5年間ROI 1.5以上」という基準を設定しており、発注システム導入もこの基準を満たすことで承認を得たと報告しています。
最後に、ROI計算は導入前の予測だけでなく、導入後の効果測定にも活用すべきです。定期的に実際の効果を測定し、当初の予測と比較することで、必要に応じた追加施策の実施や、将来の投資判断の精度向上につなげることができます。
ある製造業では、発注システム導入後、半年ごとに効果測定を行い、当初の予測と比較する「効果検証会議」を実施しています。導入1年後の検証では、人件費削減効果は予測通りだったものの、在庫削減効果が予測を下回っていることが判明し、追加の在庫最適化施策を実施することで、最終的には当初の目標を達成できたと報告しています。
段階的導入によるコスト分散
発注システムの導入において、一度にすべての機能を実装するのではなく、段階的に導入していく方法は、コスト分散と投資リスクの低減に効果的です。特に中小企業や予算制約のある企業にとって、この方法は実践的なアプローチとなります。
段階的導入の基本的な考え方は、最も効果の高い、または最も緊急性の高い機能から順に導入していくことです。これにより、初期投資を抑えつつ、早期に効果を実感できるようになります。
ある中小製造業では、発注システムの導入にあたり、以下のような4段階の計画を立てました:
第1段階(1年目):基本的な発注書作成・管理機能と承認ワークフロー 第2段階(2年目):取引先ポータルと納期管理機能 第3段階(3年目):在庫管理システムとの連携と自動発注機能 第4段階(4年目):分析・レポーティング機能の強化
この計画により、各段階で約1,000万円の投資で済み、一括導入時の4,000万円の初期投資を分散することができました。また、各段階での効果を確認しながら次の投資を決定できたため、経営層の継続的な支持を得やすかったと報告しています。
段階的導入のもう一つのメリットは、ユーザーの習熟度を段階的に高められることです。一度にすべての機能を導入すると、ユーザーの学習負担が大きくなり、抵抗感や混乱を招く恐れがあります。
ある電機メーカーでは、最初は基本的な発注機能のみを導入し、ユーザーがその操作に慣れた後、より高度な機能を追加していく方針を採用しました。この方法により、各段階でのユーザーの抵抗感を最小化し、スムーズな導入を実現できたと報告しています。また、各段階での問題点や改善要望を次の段階に反映できたことも大きなメリットだったとしています。
段階的導入を成功させるためには、全体のロードマップを明確にし、各段階の目標と評価基準を設定することが重要です。「とりあえず始めてみる」という曖昧なアプローチではなく、長期的なビジョンに基づいた計画的な導入が必要です。
ある機械メーカーでは、5年間の発注システム導入ロードマップを作成し、各段階での具体的な目標(例:第1段階では発注処理時間30%削減、第2段階では納期遵守率10%向上など)を設定しました。また、各段階の終了時に効果測定を行い、次の段階への移行判断の材料としました。この方法により、投資効果を確実に把握しながら段階的に進められたと報告しています。
また、段階的導入においては、将来の拡張性を考慮したシステム選定が重要です。初期段階では必要最小限の機能でも、将来的な機能拡張が容易なアーキテクチャを持つシステムを選ぶべきです。
ある製造業では、初期段階では基本的な発注機能のみを導入しましたが、システム選定時に将来的な拡張性を重視し、モジュール型のアーキテクチャを持つシステムを選びました。これにより、後続段階での機能追加がスムーズに行え、追加開発コストも最小限に抑えられたと報告しています。
段階的導入のリスクとしては、全体最適の視点が失われる可能性があることです。部分最適を積み重ねても全体最適にならない場合もあるため、常に全体ビジョンとの整合性を確認することが重要です。
ある電子部品メーカーでは、段階的導入の過程で、個別の最適化に注力するあまり、システム間の連携が複雑化してしまう問題が発生しました。この経験から、各段階の計画時に全体アーキテクチャとの整合性を確認する「アーキテクチャレビュー」のプロセスを導入し、後続段階でのスムーズな統合を実現できたと報告しています。
さらに、段階的導入においては、各段階での成功体験を組織内で共有し、次の段階へのモチベーションにつなげることも重要です。小さな成功を積み重ねることで、組織全体の変革への意欲を高められます。
ある製造業では、各段階の完了時に「成果発表会」を開催し、達成した効果や学んだ教訓を全社で共有しました。また、貢献度の高かった従業員を表彰する制度も設け、プロジェクトへの参加意欲を高める工夫を行いました。これにより、長期にわたるプロジェクトでありながら、組織のモチベーションを維持できたと報告しています。
コスト面では、段階的導入により、初期の効果を次の投資に活用する「自己資金化」も可能になります。つまり、第1段階での効果(コスト削減など)を第2段階の投資に充てるという好循環を作り出せます。
最後に
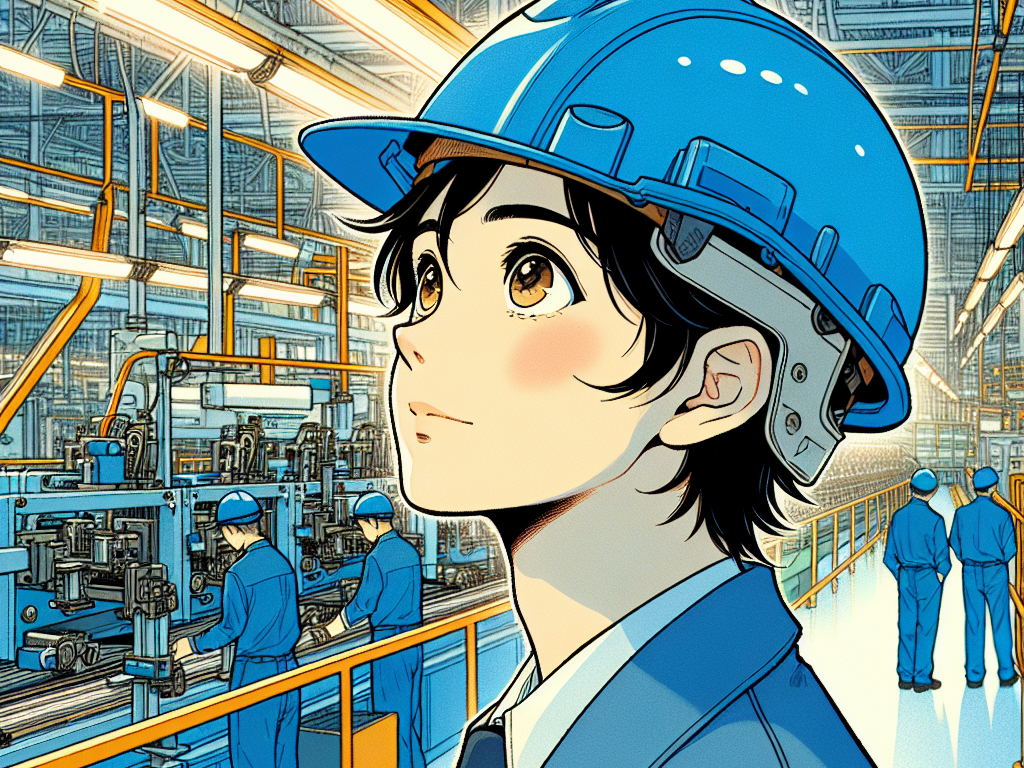
製造業における発注業務効率化は、単なる業務改善の枠を超え、企業の競争力強化と持続可能な成長を支える戦略的取り組みです。本記事では、現状と課題の分析から始まり、効率化のメリット、システム選定のポイント、実装手順、最新技術の活用、成功事例、そして未来展望まで、包括的に解説してきました。
発注業務効率化の取り組みを成功させるためには、技術的側面だけでなく、業務プロセス、人材、組織文化など、多面的なアプローチが不可欠です。特に重要なのは、「発注業務を戦略的機能として位置づける」という視点です。効率化によって生まれた時間とリソースを、より付加価値の高い戦略的活動に再投資することで、調達部門の役割を「発注処理係」から「戦略的パートナー」へと進化させることができます。
また、持続可能性の観点も今後ますます重要になります。環境負荷の低減、サプライチェーンの透明性確保、人権尊重、地域社会との共生など、SDGsに代表される社会的価値を発注業務に統合することは、社会的責任を果たすとともに、長期的な企業価値向上にも貢献します。
発注業務効率化の取り組みは、一度のプロジェクトで完結するものではありません。テクノロジーの進化、ビジネス環境の変化、社会的要請の高まりに応じて、継続的に進化させていく必要があります。そのためには、本記事で提案した段階的なロードマップと持続的な改善のための組織体制が重要な役割を果たすでしょう。
最後に、発注業務効率化の本質は「テクノロジーの導入」ではなく「価値の創造」にあることを強調したいと思います。効率化によって削減されたコストや時間、向上した精度や可視性、強化されたサプライヤー関係など、様々な形で生み出される価値が、最終的には企業の競争力と持続可能性を高めることにつながります。
製造業が直面する厳しい競争環境と急速な変化の中で、発注業務効率化は避けて通れない重要課題です。本記事が、その取り組みを検討・推進する皆様にとって、有益な指針となれば幸いです。